労働災害を防止するための8つの取り組み|労災をなくすために今すぐできる具体的な対策とは
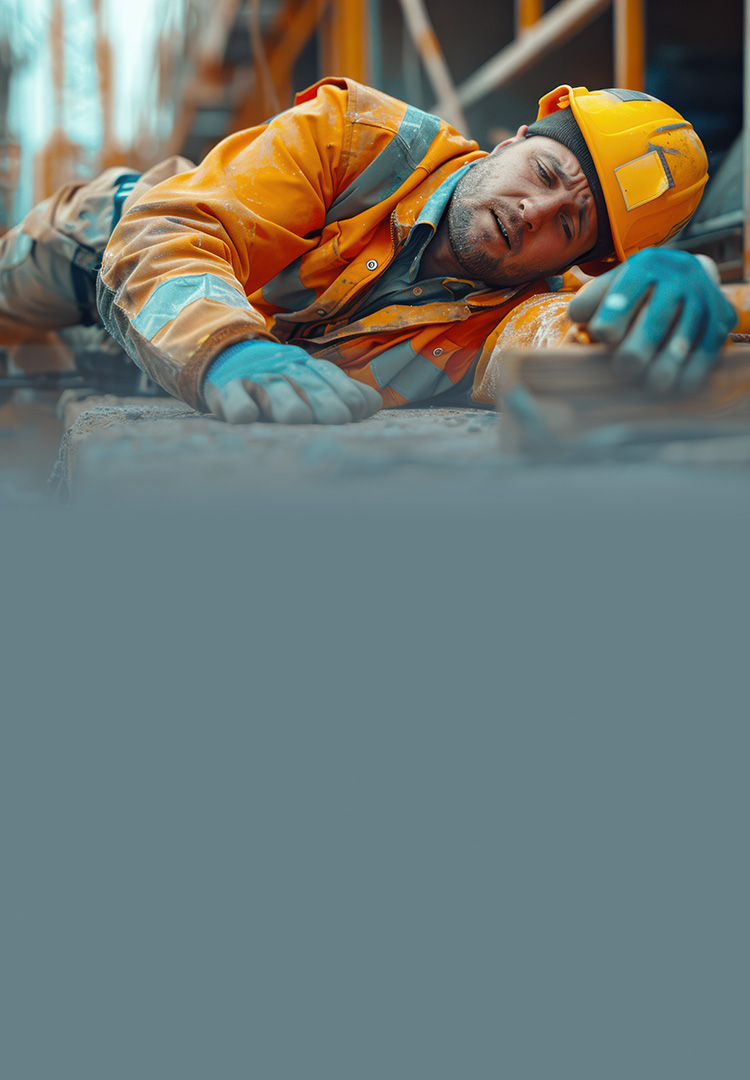
労災は、被害を受けた本人だけでなく企業にもダメージを与える重大な事故ですが、各企業の取り組みにより、労災による死亡者数は年々減少傾向にあります。とはいえ、いまだ労災は発生し続けており、死亡者も毎年700人以上発生しているのが現状です。それゆえに、労災防止の取り組みは全企業における継続的な課題として重要視されています。
本記事では、労災防止の基本や発生原因、労災をなくすための方法について解説します。「注意しているから問題ない」といった考えが労災の要因にもなるため、褌を締め直す気持ちで本記事を参考にしてみてください。
公開日:2025年4月14日
目次
- 労働災害防止の基本
-
労働災害が発生する主な原因
- 「不安全行動」と「不安全状態」の発生
- 従業員のメンタルヘルス
-
労働災害防止策の例
- 転倒
- はさまれ・巻き込まれ
- 墜落・転落
- 飛来・落下
-
労働災害をなくすには?
- ヒヤリ・ハット活動を実施する
- 危険予知活動(KY活動)を実施する
- 安全当番制度を設ける
- リスクアセスメントを実施する
- 4S活動を行う
- 安全衛生教育の徹底
- 職長再教育を行う
- 労働環境を見直す
- まとめ
労働災害防止の基本
労働災害防止の取り組みにおける基本は、労働安全衛生関係の法令を遵守し、法令に従った対策をとることです。労働安全衛生関係法令とは、職場における労働者の安全と健康を確保し、快適な職場環境を形成することを目的とした法律および関連法規の総称です。
労働安全衛生関係法令では、事業者に対して以下の措置を義務付けています。
危険防止の措置 | 機械設備を使用して作業を行う場合、機械の動作範囲に身体の部位が入らないようにするため、柵や覆いなどを設けること。 火災、爆発の危険性のある物を取り扱う場合、換気を行う、火気を使用しないなどの措置をとること。 |
---|---|
健康管理の措置 | 事業者は、従業員に対して年に1回、定期健康診断を実施すること。また、従業員を有害な業務に就かせる場合には、6カ月以内に1回、特殊健康診断を実施すること。 |
安全衛生管理体制の整備 | ①安全衛生推進者または衛生推進者の選任従業員数10人以上50人未満の事業場では、安全衛生推進者または衛生推進者を選任し、危険防止の対策や教育、健康診断などの安全衛生の業務を担当させること。②作業主任者の選任プレス機械や木材加工用機械による作業など、危険または有害な作業を行う場合には、作業主任者を選任し、作業員の指揮、機械設備の点検等を行わせること。③従業員の意見の聴取従業員の意見を聞きながら安全衛生対策を進めること。 |
安全衛生教育の実施 | 従業員を雇い入れたときなどには、安全衛生のための教育を行うこと。(教育の内容)・機械、原材料、保護具などの取扱方法・作業手順・事故時における応急措置
|
つまり、安全環境を管理するための人材・部署を設置し、各従業員に安全の重要性と安全に働く具体的な方法を教育することが、労働安全衛生関係法令においては重要なポイントとなります。
設備の危険な位置に立ち入らない、健康診断等を実施して従業員の健康を維持するといったことも法令で決められていますが、これらは企業が実施すべき義務付けられた取り組みです。各従業員の安全・危険に対する考え方は、労災に繋がる大きな要因であるため、確実に発生件数をゼロに近づけるためには教育・管理は欠かせません。
労働災害を未然防止する監視カメラとAI画像解析の活用法とは?
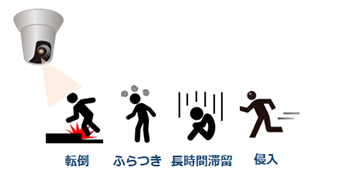
労働災害の未然防止・再発防止を実現するために、監視カメラやAI画像解析をどう活用するのか?をPDF資料に詳しくまとめました。
労働災害が発生する主な原因
労働災害が発生する主な原因は以下の2つがあります。
- 「不安全行動」と「不安全状態」の発生
- 従業員のメンタルヘルス
不安全行動や不安全状態はともに危険を誘発する行動と環境です。これらの行動と環境が常態化していると、発生するべくして労災は発生するため迅速な改善が求められます。
また、最新の注意を払っていても従業員のメンタルヘルスの状態によっては労災を誘発します。常に高い意識であることを促す必要はありませんが、メンタルヘルスが原因で労災が発生しないような取り組みは企業側にとっても大切です。
「不安全行動」と「不安全状態」の発生
「不安全行動」と「不安全状態」が発生した際に労災は発生しやすくなります。それぞれの意味は以下の通りです。
- 不安全行動:労働者本人または関係者の安全を阻害する可能性のある行動を意図的に行うこと
- 不安全状態:機械や物が不安全な状態のことで、事故が発生しうる状態、事故の発生原因が作り出されている状態
不安全行動は「慣れているから大丈夫」「これくらいいつもやっていることだから」といった気持ちで、危険であるにもかかわらず横着して行動してしまうことを指します。不安全状態は、道具が劣化していて危険な状態、作業空間が散らかっており安全な行動ができない状態、といった環境を指します。
注意しているにもかかわらず労災が発生するのではなく、作業者の安全に対する意識の低さや危険と隣り合わせの環境が労災を発生させてしまうのです。「発生するべくして発生する」典型的な労災が発生する原因といえます。
従業員のメンタルヘルス
人は様々な要因によって気持ちが浮き沈みするもので、何かしらの理由で気持ちが落ち込んでいる時は注意力が低下しやすいです。注意力が低下すると、安全に対する意識も低下してしまうため労災の要因にもなります。
作業者に悪気はなくても、メンタルの状態に問題があれば「うっかり」「ぼんやり」「勘違い」が要因でミスが発生する可能性はゼロではないため気を付けなければいけません。
「企業側がそこまで気にする必要があるのか?」と疑問に思う人もいらっしゃるかとは思いますが、結局労災が発生すればそれは企業の責任になります。そのため、企業は各従業員のメンタルヘルスに気を配り、それが要因で労災が発生しないように努めなければいけません。
企業側でメンタルヘルスに対応した部署を作るのも一つの方法ですが、難しい場合には「こころの健康相談統一ダイヤル」など厚生労働省が実施している相談窓口を推奨するというのもおすすめです。
労働災害防止策の例
労災を防止するうえで、具体的な防止策を知っておくことは重要なポイントです。何も知らずに対策をするよりも、様々な防止策を知ったうえで自社の防止策としてアレンジした方が、より防止確率の高い策となります。
労働災害が発生する場面 | 防止策の例 |
---|---|
転倒 |
|
はさまれ・巻き込まれ |
|
墜落・転落 |
|
飛来・落下 |
|
上記の労災が発生する場面は厚生労働省の「労働災害の現況と死亡災害事例」から発生が多いものをピックアップして記載しています。すべてに共通しているのは「教育」です。
環境や仕組みとして事故を防げればそれが一番ですが、人が起こす事故も多いため、危機管理能力を育てるための教育は欠かせません。定期的に社内研修などをして、どのような場所に危険が潜むのか再認識できるような場を企業側が設けるようにしましょう。
転倒
転倒はすべての現場において発生する可能性のある事故です。転倒の要因は様々で、主な例として以下のようなものがあります。
- 床の状態が悪い(濡れている、油がこぼれているなど)
- 段差がある
- 通路が狭い・ものが散乱している
- 暗くて足元が見えづらい
- 手すりが設置されていない
- 疲労で足腰が弱っている
他にも、転倒リスクに対する認識不足などがあり、あらゆる側面に対して防止策を設けないと対策が難しい事故の代表ともいえます。防止策の種類も色々とあるため、以下の防止策の例を参考に自社の状況にあわせて検討する必要があります。
- 床面の清掃・整理整頓を徹底
- 滑り止めマットや手すりを設置
- 照明を適切に設置・管理
- 疲労をためないように休憩時間を確保 など
また、注意すること自体を意識づけするのも重要であるため、通路の壁などに転倒注意の看板を貼り付けておくのもおすすめです。
労働災害を未然防止する監視カメラとAI画像解析の活用法とは?
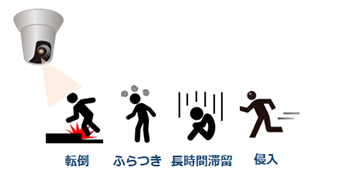
労働災害の未然防止・再発防止を実現するために、監視カメラやAI画像解析をどう活用するのか?をPDF資料に詳しくまとめました。
はさまれ・巻き込まれ
はさまれ・巻き込まれは、主に機械を取り扱う現場で発生しやすい事故です。例えば、ある印刷機の清掃をしていた際、機械内部のほこりが気になったため掃除していたところ、誤って機械が作動して頭がはさまれるという事故があったとします。このようなケースは珍しくなく、機械の電源を切らずに清掃をしていたことで事故の発生に至るケースが多いです。
はさまれ・巻き込まれは、完全に作業前の確認不足が要因であるため、以下の点に気を付けることが防止策となります。
- ささいな作業であっても、危険が伴う可能性がある場合は必ず機械を止める(もしくは非常停止ボタンを押しておく)
- 機械が作動しないように止めておく重要性を従業員に教育しておく
- 危険部分に近づくと警報が鳴るような仕組みを作っておく
- 機械をいじる際の注意看板や作業手順書などを作成しておく
機械の機能を変更しなければいけない手間やコストが発生する可能性もありますが、事故が発生した方が莫大な不利益を被るため、惜しまずに対策しておくことを推奨します。
墜落・転落
墜落・転落は高所での作業だけでなく1~2メートル程度の高さの作業でも発生します。低い場所からでも転落すれば、打ちどころによっては死亡事故となるため細心の注意を払うことが重要です。具体的な防止策には以下のようなものがあります。
- 安全帯を付ける
- 転落する可能性のある穴等がある場合は必ず簡単に取れないフタ等で塞ぐ
- ヘルメットを着用する
- 上に登って作業をする際の危険性について事前に教育しておく
高所の作業は安全帯の着用が一般化していますが、低い場所での作業の場合は基本的に着用していないことが多いです。そのため、低い場所であっても危険があることを教育しておくことが重要です。仮に頭から落ちなくても、着地の仕方次第では足の骨折等を招く要因になります。
飛来・落下
飛来・落下は様々な業務で発生しやすいです。例えば、走行中のトラックからモノが落下して後ろの車に衝突する事故や、機械をクレーンで吊っていたところで留め具が外れて機械が落ちる事故などがあります。どれも人が巻き込まれると命に関わる重大事故であるため、徹底した防止策が求められます。具体的な防止策は以下の通りです。
- 玉掛けの資格がない人に吊り作業をやらせない
- 安全確認を実施したうえで作業に入るように教育する
- 落下物が発生する可能性を予測して対策をルール化する
飛来・落下は様々な業種で発生するため、「この策を講じておけば絶対に大丈夫!」といったものは存在しません。したがって、落下する危険性のあるものを予測し、企業全体でリスク管理を徹底することが重要です。
教育ももちろん重要で、わずかでも飛来・落下が発生する可能性があるものに対して、細かく指摘・注意できるようなアンテナを張れるように教育することも欠かせません。
労働災害をなくすには?
ここまで、労災の具体的な事例に対する防止策を紹介しましたが、続いては前項の事例を含む全ての労災に対する対策方法を解説します。ご紹介する対策方法は以下の8種類です。
労働災害をなくすための対策方法
- ヒヤリ・ハット活動を実施する
- 危険予知活動(KY活動)を実施する
- 安全当番制度を設ける
- リスクアセスメントを実施する
- 4S活動を行う
- 安全衛生教育の徹底
- 職長再教育を行う
- 労働環境を見直す
ヒヤリ・ハット活動やKY活動は、危険を伴う現場に携わる人であれば、一度は聞いたことのあるワードではないでしょうか。全ての対策方法を同時に進めるのは現実的ではないため、まずは現状の現場環境等を踏まえて、取り入れられるものから実施していくようにしましょう。
ヒヤリ・ハット活動を実施する
ヒヤリ・ハット活動とは、事故には至ってないが事故になりそうな事象(ヒヤッとした事象)や危ないかもしれないと感じたこと(ハッとしたこと)の記録を通して、そのような事態が再度発生しないように努める安全衛生活動のことです。
一つの重大事故の背景には、300の無事故で済んだ事象があるとされており(ハインリッヒの法則)、そのような無事故の事象を減らしていくことが重大事故の防止に繋がります。
例えば、「機械の上に工具が置きっぱなしになっていて、事故にはならなかったが機械の中に落下したら重大な事故になっていたかもしれない」といった事象があったとします。このような事象に対して、ただ注意するのではなく「注意看板の作成」や「工具使用時のマニュアル」を作成することで、具体的な対策として着地させることが可能です。
ヒヤリ・ハット活動は工場などの現場だけでなく、子どもを預かる保育園などでも活用されている方法で、わずかなケガも発生させない対策方法として知られています。
危険予知活動(KY活動)を実施する
危険予知活動(KY活動)とは、危険があるとされる箇所を予測したうえで、その箇所に注意して作業に入る活動のことです。主に工場や建設現場など、危険な箇所が予め予測できるような現場で行われることが多く、決められた対策に基づいて安全行動に努めるように朝礼で確認します。
KY活動の代表的な方法として「4ラウンド法」というものがあり、以下の順で進めます。
-
現状把握:現状を分析して想定されるリスクを洗い出す
-
リスクの整理:洗い出したリスクのなかで優先度が特に高いものを選定する
-
対策方法の決定:優先度の高いリスクの対策について担当者同士で提案・精査する
-
目標設定:決まった対策を目標にして、作業前の確認事項に組み込み、それを意識しながらその日の作業にあたることを徹底する
ここまでが基本的なKY活動に該当しますが、現場によっては作業前の朝礼時に「~~よし!」といった指差し呼称を行うなど、さらに工夫してKY活動をしているところも多くあります。重要なのは作業前に危険事項の確認を作業員同士で実施することであり、危険に対する意識を高めて労災防止に努めなければいけません。
KY活動(危険予知活動)の4つの課題や悩みを解消する方法
KY活動(危険予知活動)の4つの課題
-
レポートの項目が思いつかない(ネタが出せない)
-
KY活動を効率よく進められない
-
危険行動が減らない
-
KY活動の成果がみえない
AIカメラで危険行動を自動検知して解決

4つの課題を解決するAIカメラの活用方法をPDF資料でご紹介
安全当番制度を設ける
安全当番制度とは、安全を管理する役職の人ではなく、実際に現場にいる作業員が当番制で安全パトロールや安全活動の進行役を行う制度のことです。全ての作業員が担当することになるため、一人ひとりの安全に対する意識を高めるだけでなく、その意識を維持することにも繋がります。
労災の多くは作業員の気のゆるみなどから発生するため、安全当番制度は効果の高い対策方法です。
安全当番制度を実施する際は、その制度の為に新たに安全活動を増やす必要はありません。朝礼の中で実施している「指差し呼称」を毎日順番に担当するだけでも意識の向上に繋がるため、現在行っている安全活動を担当制にするだけでも効果が見込めます。
リスクアセスメントを実施する
リスクアセスメントとは、現場における作業や業務に潜む危険を特定し、そのリスクの大きさを評価したうえで、労働災害を未然に防ぐための対策を検討・実施する一連のプロセスです。取り組むことで潜むリスクを明確化し、そのリスクに対する意識を高められる効果が見込めます。
なお、リスクアセスメントは労働安全衛生法で努力義務とされており、全ての企業が取り組みを推奨されています。取り組みの詳細は以下の通りです。
-
リスクの特定:職場環境や作業内容、使用する機械設備、化学物質など、あらゆるものからリスクをリストアップ。
-
リスクの評価:特定したそれぞれのリスクを、発生する可能性や発生した場合の想定被害度を考慮して評価。リスクレベルを「低・中・高」などの表記で評価。
-
リスク低減対策の検討・実施:評価したリスクのレベルに応じて、優先順位を付け、効果的な対策を検討・実施。
-
リスクアセスメント結果の記録・見直し:リスクアセスメントの結果を記録し、定期的に見直すことで、対策の効果を確認し、必要に応じて改善。
リスクアセスメントは、現場担当者や管理者など、複数の関係者が集まって意見を交換しながら実施していくことが重要です。様々な役職の担当者が集まって取り組むことで、多角的な視点からリスクアセスメントを実行できます。
4S活動を行う
4S活動とは、職場環境を改善し、安全で効率的な作業環境を維持するための活動を指します。4SのSはそれぞれ以下の意味を持ちます。
- 整理:不要なものを捨てる、または処分し、必要なものだけを残すこと。
- 整頓:必要なものを決められた場所に置き、いつでも取り出せるようにすること。
- 清掃:職場をきれいに掃除し、汚れやゴミのない状態にすること。
- 清潔:整理・整頓・清掃を維持し、常に清潔な状態を保つこと。
4S活動によって整理整頓された職場は、つまずきや転倒などの事故を防ぎ、安全な作業環境を実現します。また、きれいに清掃されていることで機械の故障や火災などのリスクも抑えられます。
労災の多くは、ルールの整備不足や従業員の安全に対する意識の低さから来るため、事故を防ぐためには意識を高く保ち続ける環境も大切です。4Sを意識した現場づくりを続ければ、整理整頓された現場で自然と気が引き締まるだけでなく、汚さないように各々が気を付ける効果も期待できます。
安全衛生教育の徹底
安全衛生教育とは、職場における労働災害や健康障害を防止するために、労働者に対して安全衛生に関する知識や技能を習得させるための教育のことです。安全衛生教育は、チェーンソーを扱う林業などのように危険な作業が伴う場合に実施が義務付けられています。
具体的には、以下のような教育を実施しなければいけません。
-
雇い入れ時の安全衛生教育
新しく雇い入れた労働者に対して、職場の安全衛生に関する基本的な知識や、従事する業務に関する安全衛生上の注意点などを教育。
-
作業内容を変更する場合の安全衛生教育
労働者の作業内容を変更する場合、変更後の作業に関する安全衛生教育。
-
職長・安全衛生責任者などに対する安全衛生教育
職長や安全衛生責任者など、安全衛生に関する指導・監督を行う立場にある者に対して、必要な知識や能力を習得させるための教育。
-
危険有害業務従事者に対する特別教育
フォークリフトの運転、プレス機械の操作、有機溶剤の取扱いなど、危険性や有害性の高い業務に従事する労働者に対して、それぞれの業務に応じた特別教育を実施。
これらの教育は定期的に実施することで安全衛生意識を高められます。また、職場環境や作業内容に変化が生じた際にも、それに応じた教育を実施しましょう。
職長再教育を行う
職長再教育とは、すでに職長としての経験を持つ労働者に対して、安全衛生に関する知識や技能を再確認・更新するための教育です。一定の要件を満たす建設現場に入った事業者は、安全衛生責任者を選任しなければならないとされているため、職長の職務に再度就く人に対して教育を実施することで安全管理を徹底します。
職長再教育では、職場の長として機能するための基本的な管理能力や指導力を育成することを目的に教育が実施されます。コミュニケーション能力や意思決定能力、安全、労使関係などが主な教育内容で、教育を通して労災の防止に努めなければいけません。
主に建設現場において求められている教育であるため、建設業に携わる業者は確実に押さえておく必要があります。なお、下請け業者に対してもこの教育の実施は求められています。
関係請負人(下請け)として建設現場に入る事業者は、雇用している職長等及び安全衛生責任者に対し初任時に教育を受けさせるとともに、概ね5年ごと又は機械設備等に大幅な変更があったときにも再教育を受けさせるようにしてください。
労働環境を見直す
労働環境の見直しは定期的に検討すべき取り組みの一つです。具体的には、時間外勤務や休日出勤の減少や、有給休暇取得の促進などが挙げられます。
労災は、作業員の気のゆるみからくるものも多いですが、ゆるみの発生は慢心だけでなく疲労なども要因の一つと考えられます。そのため、企業側は作業員が万全のコンディションで仕事に着手できるように労働時間の管理等は徹底する必要があります。
平成31年4月1日に行われた安全衛生法の改正では、社員の1ヶ月の時間外・休日労働時間が80時間(改正前は100時間)を超えた場合、医師による面接指導の実施も義務付けられ、国としても労働環境を重視しているのが分かります。
納期等の兼ね合いで残業等をせざるを得ないケースも十分にあるかとは思いますが、従業員の新たな雇用や客先との納期調整などによって最大限の努力をしなければいけません。
労働災害を未然防止する監視カメラとAI画像解析の活用法とは?
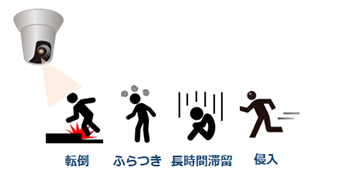
労働災害の未然防止・再発防止を実現するために、監視カメラやAI画像解析をどう活用するのか?をPDF資料に詳しくまとめました。
まとめ
労災は一度発生するだけで企業に大きなダメージを与える可能性があります。それゆえに、労災防止の取り組みは全企業が重視している取り組みの一つで、「安全第一」で効率はその次といった方針にしている企業も少なくありません。
労災は転倒やはさまれ、墜落、落下といった事故が毎年多く報告されているため、これらの事故が潜在的な可能性としてある場合には、優先的に対策することを推奨します。機械の設備で対策できるものはコストよりも安全重視で可能な限り設備変更に努め、人の意識レベルが重要な対策になる場合は教育を通して対策を図りましょう。