不安全行動とは?
不安全状態との違いや、なくすための具体的な対策方法を解説
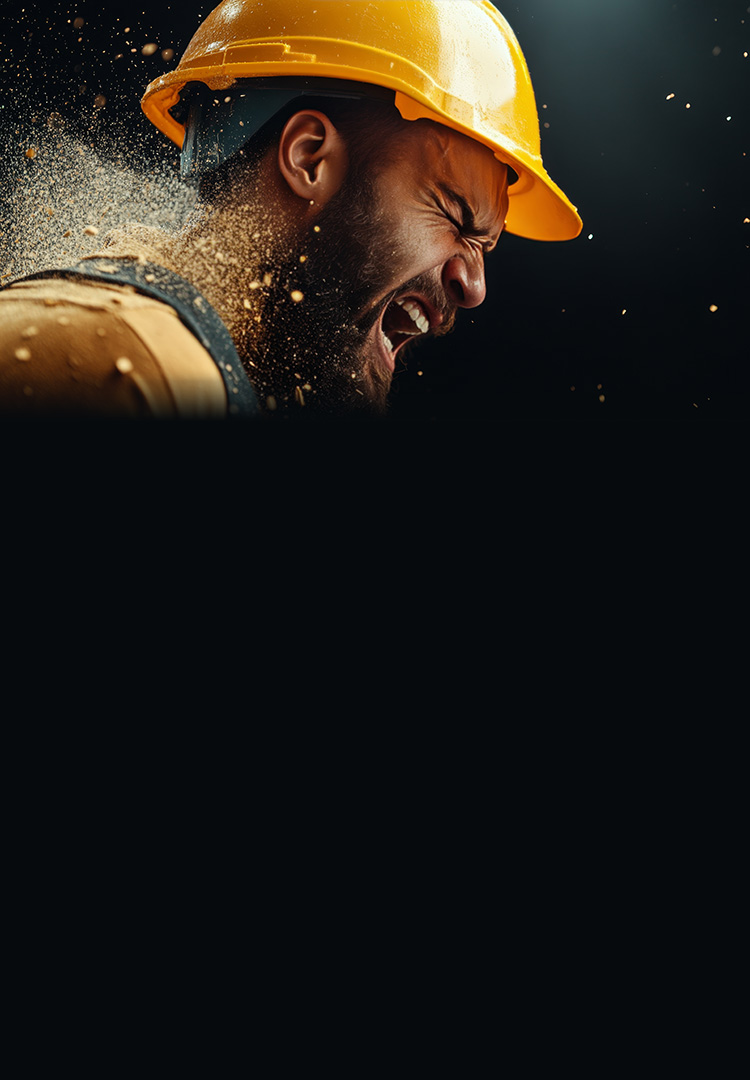
不安全行動とは、労働者本人もしくは関係者が危険にさらされる可能性のある行動を意図的に行う行動を指します。不安全行動は労働者自身の慢心や気のゆるみなどから発生する行動であるため、人材教育の段階から改善していかないと完全な解決には向かいません。
実際に事故にまでは至っていないが、作業員の行動に危険性を感じており、早急な対策を検討している人も多いのではないでしょうか。
本記事では、不安全行動の具体例や、なくすための対策方法を解説します。労災は発生してからでは手遅れであるため、これを機に万全な対策を講じられるよう、参考にしていただければ幸いです。
公開日:2025年4月14日
目次
- 不安全行動とは
- 不安全行動の具体例
- 不安全状態とは
- 不安全状態の具体例
-
ヒューマンエラーが発生してしまう要因
- 車の運転時におけるリスクテイキング行動
- インターネット上のリスクテイキング行動
-
不安全行動をなくすには?
- 設備・環境の改善
- 作業ルールの徹底とマニュアルの見直し
- 安全教育の徹底
- 管理監督者のチェック強化
- 労働環境の見直し
- まとめ
不安全行動とは
不安全行動とは、労働者または関係者を危険にさらす可能性のある行動を「意図的」にする行動のことです。国土交通省では、以下12の項目を不安全行動の例として挙げています。
労働者の不安全行動
[1]防護・安全装置を無効にする
[2]安全措置の不履行
[3]不安全な状態を放置
[4]危険な状態を作る
[5]機械・装置等の指定外の使用
[6]運転中の機械・装置等の掃除、注油、修理、点検等
[7]保護具、服装の欠陥
[8]危険場所への接近
[9]その他の不安全な行為
[10]運転の失敗(乗物)
[11]誤った動作
[12]その他
安全帯を付けて作業する、安全装置を作動させて作業する、などのようにルールを守っておけば危険な状態にならないにもかかわらず、故意的に守らず作業にあたることで労災を誘発します。ルールを守らない人の多くは、「いつもそのやり方だから」や「守らない方が効率が良いから」といった考えのもと行動しているケースが多いです。
また、[9]に該当しますが、転倒、ふらつき、酩酊状態などが原因で労災が発生するような行動も不安全行動になります。これらの行動が発生する原因は、疲労や精神的ストレスが考えられます。個人で対策するのは難しいため、「危険行動を検知できるシステム」などを活用して対策するのが効率的です。
不安全行動を検知する方法とは?
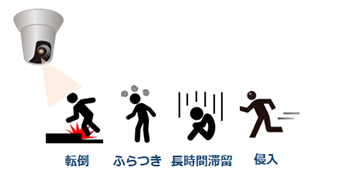
監視カメラを活用して不安全行動の自動検知とその対策を進める方法をPDF資料にまとめました。
不安全行動の具体例
前項では、国土交通省が例として挙げている12項目の不安全行動を紹介しました。以下では、それらの具体例を解説します。
不安全行動の項目 | 具体例 |
---|---|
防護・安全装置を無効にする | 機械の中に入って点検作業をする際に、安全装置を無効化しており、そのまま機械に挟まれる。 |
安全措置の不履行 | 故障した機械を修理せずに使い続けることで、事故を誘発。 |
不安全な状態を放置 | クレーンで重機を吊った状態で放置し、留め具が外れて作業員の頭に落下。 |
危険な状態を作る | 通路や作業場所に資材、工具、廃材などを放置し、それを踏んだ作業員が転倒。 |
機械・装置等の指定外の使用 | クレーンで定格荷重を超える重量物を吊り上げるなど、決められた使い方をせずに事故発生。 |
運転中の機械・装置等の掃除、注油、修理、点検等 | 回転している機械のカバーを開けて、内部の清掃を行った結果、巻き込まれる。 |
保護具、服装の欠陥 | 破損したヘルメットを使用した結果、ものにぶつかった際に頭部を負傷。 |
危険場所への接近 | 足場や高所作業床からの転落の危険がある場所へ、安全帯を着用せずに接近した結果、転落。 |
その他の不安全な行為 | 疲労や体調不良を無視して作業を続けた結果、めまい等が発生して転倒。その際に頭をぶつけてケガを負う。 |
運転の失敗(乗物) | スマートフォンの操作、通話、メールの確認など、脇見運転をした結果、交通事故を起こす。 |
誤った動作 | 足場を移動する際に、手すりにつかまらずに移動した結果、足を滑らせて転落。 |
その他 | 緊急停止ボタンの位置を把握していないことが原因で、機械が作動した際にすぐに止められず事故を誘発。 |
これらの中でも、特に「不安全な状態を放置」「危険場所への接近」といった項目は発生しやすい不安全行動です。
クレーンで機械を吊っている状態であるにもかかわらず吊った状態で他の作業に移ってしまい、放置した結果、転落するような事故は可能性として十分にあり得ます。クレーンから離れる際は必ず吊っているものを床に下ろしてから移動するなど、ルールを決めておかないと、高い確率で人を巻き込んだ事故に発展してしまうため、対策が必要です。
不安全状態とは
不安全状態とは、機械や物が不安全な状態のことで、事故が発生しうる状態、事故の発生原因が作り出されている状態のことです。例えば、道具が劣化していて危険な状態、作業空間が散らかっており安全な行動ができない状態、といった環境を指します。不安全行動は人の行動によるものでしたが、不安全状態は主に現場環境等によるものがほとんどです。
また、国土交通省は不安全状態について以下8項目を例として挙げています。
機械や物の不安全状態
[1]物自体の欠陥
[2]防護措置・安全装置の欠陥
[3]物の置き方、作業場所の欠陥
[4]保護具・服装等の欠陥
[5]作業環境の欠陥
[6]部外的・自然的不安全な状態
[7]作業方法の欠陥
[8]その他
主に物が散乱している状態や、使用する安全具が破損しているなどが不安全状態の具体例として挙げられます。そのため、不安全状態を改善するには4S(整理・整頓・清掃・清潔)を意識した現場環境の改善や、定期的な工具・設備の点検の実施が重要です。
不安全行動を検知する方法とは?
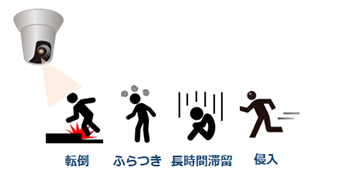
監視カメラを活用して不安全行動の自動検知とその対策を進める方法をPDF資料にまとめました。
不安全状態の具体例
不安全状態の8項目における、それぞれの具体例は以下の通りです。
不安全行動の項目 | 具体例 |
---|---|
物自体の欠陥 | 柄が抜けやすいハンマーを知っていたにもかかわらず使用して、そのまま先端が飛んでしまって人に衝突。 |
防護措置・安全装置の欠陥 | 危険な機械の可動部や高温部に、容易に接触できる状態になっており、作業員が触れてしまってケガを負う。 |
物の置き方、作業場所の欠陥 | 資材や工具、製品などを通路に放置して通行の妨げとなっており、作業員がそこで躓いて転倒。 |
保護具・服装等の欠陥 | 安全靴のつま先保護部分が破損していることによって、重機が足のつま先部分に乗ってしまった際に保護しきれずに指を負傷。 |
作業環境の欠陥 | 現場照明の電球が劣化してきており、暗い状態となっている。その結果、手元がよく見えないことにより機械や工具の異常を見落としてしまい、事故が発生。 |
部外的・自然的不安全な状態 | 地震対策が行われておらず、実際に大きな地震が発生した際に上に積んであったものが落ちてきて、人の頭に衝突して負傷。 |
作業方法の欠陥 | 作業開始前や作業中の安全確認が不十分で、危険を見逃す可能性があり、実際に作業をしたら危険な可能性がある工程で事故が発生。 |
その他 | クマ、イノシシ、ハチ、ヘビなどの害獣被害が発生する可能性がある地域において、その対策を怠った結果、ケガ人が発生する事態となった。 |
害獣や地震など外部的要因における不安全状態は、なかなか予測できないため対策が難しいです。一方で、「物自体の欠陥」や「保護具・服装等の欠陥」といった不安全状態は、現場全体で注意するように心がければ、改善が見込めます。そのため、設備の定期点検や整理整頓などをルール化して、日常的に行なうことで労災対策が可能です。
ヒューマンエラーが発生してしまう要因
労災の要因として不安全行動を挙げましたが、実際のところ人が起因の発生要因はヒューマンエラーもあります。不安全行動は「意図的」に起こした行動でしたが、ヒューマンエラーは「意図せず」に発生するミス等であるため、それぞれ対策方法が異なります。
ヒューマンエラーが発生する要因は、主に「うっかりミス」といった思いがけないトラブルなどがあります。他にも「危険と知りながらも敢行してしまう心理的な状態」であるリスクテイキングもヒューマンエラーに繋がる要因です。
リスクテイキングについては、以下に解説する「車の運転時」と「インターネット上」の二つのケースを例に挙げます。
車の運転時におけるリスクテイキング行動
車の運転時におけるリスクテイキング行動には、「運転中のスマホの操作」や「スピード違反」「通話しながらの運転」などが挙げられます。意図的に違反しようとしているわけではなくとも、警察に見つかった際には違反となるリスクを伴う行動です。
これらのリスクテイキング行動をとってしまう理由は、以下のようなものが考えられます。
- 急いでいる:時間に遅れそう、目的地に早く到着したい、という焦りからスピードを出しすぎてしまう。
- 運転に慣れている:運転経験が豊富であることから、自分の運転技術を過信し、危険な行動をとってしまう。
- ストレス:精神的なストレスを抱えている場合、攻撃的な運転になりやすい。
- 飲酒:アルコールの影響で判断力が低下し、危険な行動をとってしまう。
以上の点から、車の運転時におけるリスクテイキング行動を防止するためには、自制心の強さが最も重要であることが分かります。性格的な側面もありますが、多くの場合では「精神的な余裕のなさ」が関係してくるため、メンタルヘルスケアなど心にゆとりを持たせることが必要です。
インターネット上のリスクテイキング行動
インターネット上のリスクテイキング行動には、「SNSや掲示板での誹謗中傷」や「出所不明のフリーWi-Fiに接続」、「外出先でPCの画面が見える状態で作業する」、「セキュリティソフトを最新に更新していない」などが挙げられます。
匿名で利用できるから攻撃的になってしまう、利便性を追求した結果、リスクのことを気にしなくなってしまう、といった心理的状態がリスクテイキング行動を招いてしまいます。これらの行動を起こさないためには、以下の点に注意することが重要です。
- 個人情報を安易に公開しない
- セキュリティ対策を徹底する
- 不適切なコンテンツの投稿・共有をしない
- ネットいじめや炎上に加担しない
- 危険なサイトにアクセスしない
インターネットが利用しやすい世の中になったからこそ、利用する側は細心の注意を払わなければいけません。
以上のように、ヒューマンエラーは心の焦りや利便性の追求、リスクを負ってでも起こしたい行動がある、といった状態のときに発生しやすいことが分かります。労働現場においても同様で、少しの利便性を追求した結果、危険を伴うリスクテイキングをしてしまうなど、わざとでは無くても労災に繋がる行動を起こしてしまい、最後にはヒューマンエラーとして発生する危険をはらんでいます。
不安全行動を検知する方法とは?
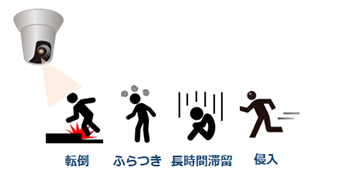
監視カメラを活用して不安全行動の自動検知とその対策を進める方法をPDF資料にまとめました。
不安全行動をなくすには?
ヒューマンエラーはリスクテイキング行動をとらないように企業側で管理・配慮することで対策が可能です。一方で、不安全行動の場合は意図的に危険が伴う行動を起こすため、半ば強制的に監視・教育する仕組みや危険がそもそも発生しにくい環境づくりが求められます。
意図的に行動を起こせないような仕組みにすることが重要であるため、以下の対策方法を参考に不安全行動の排除に努めましょう。
- 設備・環境の改善
- 作業ルールの徹底とマニュアルの見直し
- 安全教育の徹底
- 管理監督者のチェック強化
- 労働環境の見直し
設備・環境等を改善することによって、意図的に危険を犯す行動を防止することが可能です。危険が伴う行動は不便さなども要因となってくるため、設備や環境を改善して利便性の高い現場を作り上げれば、危険を伴う行動を起こす必要のない状態まで改善することができます。
また、危険を犯すこと自体の問題性を再度認識させるために、教育や管理体制を見直すことも重要です。作業員が独自の判断で危険が伴う行動を起こすため、作業員の意識を変えていくことで不安全行動を避ける自制心を育て上げられます。
設備・環境の改善
設備・環境の改善によって、危険を伴う機械操作や危険な場所へ足を踏み入れるといった事態を防げます。例えば、機械が古くて安全装置の調子が悪い機械を使用していたとします。このようなケースでは、危険とわかっていてもその機械を操作しなければ製造が進まないため、操作を続ける判断をせざるを得ません。
そこで機械の修理や入れ替えといった改善策を取れば、安全装置が正常に作動する機械へと変わるため、マニュアル通りに使用していれば危険を伴わない作業へと改善できます。危険を排除するように企業側で努めれば、不安全行動をとるきっかけが無くなるため、それが防止策となるのです。
作業ルールの徹底とマニュアルの見直し
作業ルールの徹底とマニュアルの見直しをしましょう。そもそも作業ルールは「危険を伴わない」ことは大前提として作られているため、ルール通りに作業を遂行すれば危険を伴わずにあたることができます。それでもルールを破る要因は、横着や利便性の追求といった点が考えられますが、これらは危険を犯してまで実行することではありません。
作業ルールを徹底させれば、多少作業効率が落ちる可能性はあれど、不安全行動の発生リスクを最小限に抑えられます。マニュアルについても同様で、マニュアル通りに進めれば危険が発生する可能性は低いため、遵守するよう作業員に指示する必要があります。
なお、マニュアルにおいては設備の変化や更なる良いアイデアによって改善・修正が求められるケースもあります。その時々に応じて柔軟に見直し・更新をしていけば、リスクの低減につながります。
安全教育の徹底
安全教育は従業員の危機管理能力を養うのに最適です。現場における「安全」は、管理者が一人の労働者を24時間常に監視しているわけにはいかないため、管理者が注意するだけではなかなか防ぎようがありません。
そこで安全教育が徹底されれば、作業者自身が意識的に危険を回避する行動をとるようになるため、管理者の目が届かない範囲でも不安全行動をとる可能性を抑えられます。なお、安全教育では以下のような内容を作業員に教育します。
- 労働安全衛生法の概要や事業場における安全衛生管理体制、労働災害の発生状況
- 機械・設備の操作方法や危険物・有害物の取扱い方法、作業手順、保護具の着用方法
- 新しい機械・設備の操作方法や新しい危険物・有害物の取扱い方法、変更後の作業手順
- 労働者の安全と健康を守るための指導・監督方法
- リスクアセスメントの実施方法や安全衛生管理計画の作成・実行方法
業種によって教育内容はアレンジしても問題ありません。不安全行動をとらない意識を植え付けられるように、徹底した教育が重要です。
管理監督者のチェック強化
管理監督者とは、労働者を直接指揮命令する権限を持ち、業務の遂行について責任を負う立場にある人のことです。現場の安全を維持するのも管理監督者の業務内容のひとつであり、定期的に安全状況をチェックすることで現場に危険が発生しないように努めます。
このチェック内容を強化することによって、より安全な状態を維持できるような環境づくりに繋げることが可能です。具体的には、定期チェックの頻度の増加やチェック項目の増加などの取り組みが挙げられます。
ただ闇雲にチェック項目を増やせばいいわけではなく、どの部分に危険が潜むかの分析をしたうえで必要な項目を追加しましょう。この際、現場の担当者も交えて意見を出し合えば、より現場の状況を考慮したチェックの強化が可能です。
労働環境の見直し
労働環境を見直すことによって、各作業員の精神的な余裕を生み出せる可能性があるため、一つひとつの行動に対して冷静に判断するための時間を作りやすくなります。
もちろん、性格的に冷静を保てないケースもありますが、十分な休息が取れる労働環境であれば、疲労から誤った判断をしてしまうことや、余裕がないために危険な選択をしてしまうといった事態は防ぐことができます。
また、作業員からの企業に対する不平不満が多いと、作業ルールを守らないといった行動をとる人が出てくる可能性もあります。給与に反映するなどの策は不要ですが、休憩時間を10分追加するなどして作業員から不平不満が出ないようにする取り組みが大切です。
不安全行動を検知する方法とは?
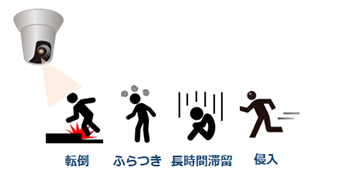
監視カメラを活用して不安全行動の自動検知とその対策を進める方法をPDF資料にまとめました。
まとめ
不安全行動は意図的に危険を含む行動をとることを指します。意図的といっても悪意があるわけではなく、「いつもやってるから大丈夫」「床が散らかってるけど跨がないと仕事ができないから跨ぐ」などのように様々な理由で不安全行動は引き起こされます。
危険な行動で済んでいるうちは問題ありませんが、それが実際に事故まで発展したら取り返しのつかない事態になってしまいます。そのため、企業は不安全行動を起こさないような現場づくり、人材教育が欠かせません。特に教育は、各作業員が危険を自ら察知して正しい行動をとるためにも必要な労災防止策ともいえます。