再発防止策の立て方と具体例|作業ミスやトラブルが発生する根本原因からわかりやすく解説
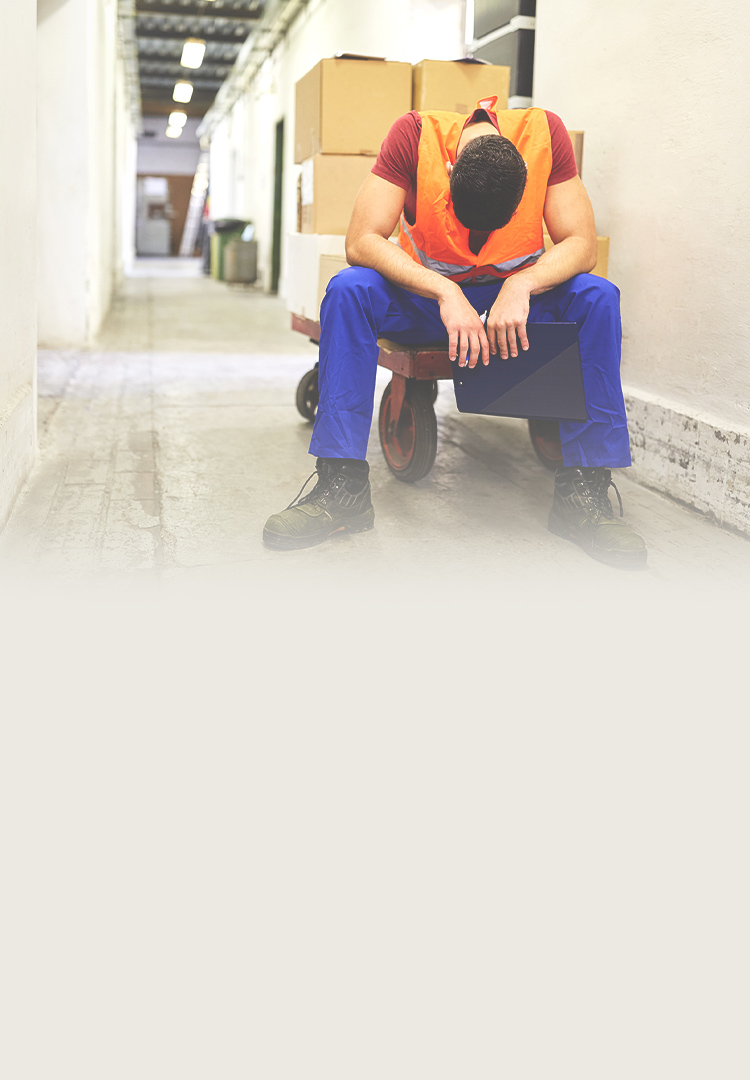
製造業、建築業、サービス業など、どんな業種でも作業ミスやトラブルは発生します。そのため、各企業のほとんどが作業ミスの発生から学んで、再度発生しないように対策を施します。
作業ミスやトラブルの再発は、場合によっては顧客の信用を大きく損失することに繋がります。適切な再発防止策を取れば、同じようなミスを二度繰り返すことは防げるため、正しい知識を身に着けて再発防止策に取り組みましょう。
本記事では、そもそも作業ミスやトラブルが発生する原因は何なのか、具体的にどのようにして再発防止策を立てれば良いのか、といったことについて解説します。ミスの繰り返しに悩んでいる方や、現場管理の強化などについて検討している方はぜひ本記事の内容を参考にしてみてください。
労働災害を未然防止する監視カメラとAI画像解析の活用法とは?
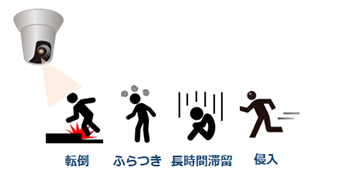
労働災害の未然防止・再発防止を実現するために、監視カメラやAI画像解析をどう活用するのか?をPDF資料に詳しくまとめました。
目次
- 作業が属人的
- 業務ルールの周知不足
- コミュニケーション不足
- 確認不足
- 根本的な原因を究明する
- 再発防止の重要度を図る
- 対策方法を講じる
- マニュアル化する
- 機会最小を実行する
- RPAなどのシステムを導入する
- 作業やルールをわかりやすくする
- 個人ではなく仕組みで防止する
- ダブルチェックを行う
- 「侵入検知サービス」の概要
- 「危険行動検知サービス」の概要
- 活用できる理由
再発防止とは
再発防止とは、職場における作業ミスや品質上のトラブル、労働災害などを繰り返し発生させないように具体的な策をもって取り組むことです。再発防止の取り組みは、顧客の信用の損失を防ぐことや従業員の安全を確保することに繋がります。
再発と記載してあるように、一度発生したトラブル等に対する策を講じるのが通常で、PDCAを回しながら職場内で再発を防ぐために取り組むケースがほとんどです。その具体的な方法はトラブルやミスの内容によって変わってくるため、その都度職場内で話し合って最善な策を追求しなければいけません。
作業ミスやトラブルが発生する原因
再発防止に取り組むのなら、まずは「なぜ作業ミスやトラブルが発生するのか」を確認することが大切です。原因を掴むことができれば、より効果的な対策が立てられます。原因は細かく分けると色々とありますが、本記事では以下の4つを主な原因としてご紹介します。
作業ミスやトラブルが発生する原因
- 作業が属人的
- 業務ルールの周知不足
- コミュニケーション不足
- 確認不足
作業ミスなど業務の中で発生するものは、属人的な作業や作業工程のルール化がされていないといった理由であることが多いです。また、コミュニケーションが必要な職場では、報連相が十分になされておらずミスやトラブルに繋がってしまったということも珍しくありません。
作業が属人的
作業が属人的であるということは業務の標準化がされていないことを意味します。業務標準化が出来ていないと「効率的な作業が実施できない」「安全面を考慮したうえでの作業が実行されない」などの問題が発生します。一部の職業によっては「その人にしかできない作業」があることも考えられますが、基本的には属人的な作業が作業ミスやトラブルの原因となりやすいです。
また、属人的な作業がある職場には、以下のような特徴があります。
- 作業手順やルールが明確にされていない
- 担当者の経験やスキルに依存する作業がある
属人的な作業があるかどうかの認識が無い場合には、上記の2つに該当するかどうか確認してみてください。該当する場合は属人的な作業があるかもしれません。
業務ルールの周知不足
ここで言う業務ルールとは、作業工程における各ルールのことを指し、ルールの内容は職場によって異なります。例えば、危険な場所には入らない、特定の作業中は安全手袋をつける、といったルールがあります。
ルールを作っても周知していなければ意味がありません。職場にいる全従業員がルールを把握し、それに倣って作業を実施できるように仕組みを作ってください。
ルールを守ることができれば、結果的に従業員全員の作業内容や行動範囲を統一していくことが可能となるため、想定外の作業ミス等が発生しにくくなります。一度発生したミスに対してもルールを作っておけば、二回目の発生を防ぐことができるでしょう。
コミュニケーション不足
従業員同士のコミュニケーションが不足すると、情報の周知ができずに作業ミスが発生する可能性があります。特に引き継ぎ業務があるような職場に関しては、コミュニケーション不足が品質不良や作業ミスに繋がることも珍しくありません。
コミュニケーションは従業員に任せてしまうと、各々の関係性で十分に実施しない可能性があります。そういった側面も踏まえて、管理側はコミュニケーションを意識的にとるようなルールや仕組みを作っておくと良いでしょう。
例えば「チーム内でグループLINEを作る」「専用の掲示板を作って必ずその日の出来事などを記入するようなルールを作る」といったものが挙げられます。従業員同士の関係性に関わらず円滑なコミュニケーションが取れるように努めましょう。
確認不足
何事においてもそうですが、確認不足は作業ミスや事故のもとです。特に建築業や製造業など高所に上る作業や機械を動かす作業がある場合には、指差し呼称による確認は必須になります。
この確認作業は現場担当者だけでなく管理する側にも求められます。例えば「現場に危険な場所は無いか?」「従業員が危険な作業はしていないか?」といった確認は管理者が実施するべき項目です。作業員と管理者の双方が危険や作業ミスが発生しないように確認作業を実施することが大切です。
労働災害を未然防止する監視カメラとAI画像解析の活用法とは?
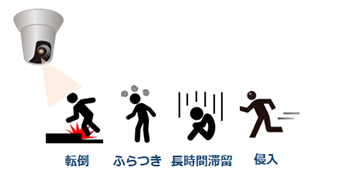
労働災害の未然防止・再発防止を実現するために、監視カメラやAI画像解析をどう活用するのか?をPDF資料に詳しくまとめました。
再発防止策の立て方
続いては作業ミスやトラブルが再発しないための防止策の立て方について解説します。具体的な方法は以下の通りです。
再発防止策の立て方
- 根本的な原因を究明する
- 再発防止の重要度を測る
- 対策方法を講じる
先述したような原因を把握しておくことで、根本からミスやトラブルが発生するのを防げます。表面的にミスを抑え込むだけでは、根本的な解決にならないので気を付けましょう。
根本的な原因を究明する
再発防止策を立てるためには、まずは発生したミスやトラブルの原因を探るところから始めます。根本的な原因を究明できないと、再発を防げない可能性が高くなるので気を付けましょう。
根本的な原因を究明するためには、「なぜ?」を繰り返して原因を深堀していくと良いでしょう。例えば「注文数に対して納めた製品の数が間違っていた」という事故があったとします。この事故に対して「なぜ?」を繰り返していくと以下のように根本的な原因を突き詰めることができます。
ミス内容 | 注文数に対して納めた製品の数が間違っていた |
---|---|
なぜ?① | 担当者が注文数の認識を間違えていた |
なぜ?② | 生産管理部門との情報交換が出来ていなかった |
なぜ?③ | 普段から定期的に注文数に対するすり合わせをするルール等が作られていなかった |
今回は3回の掘り下げですが、内容によってはもっと掘り下げられるケースもあります。原因を追究するうえで「なぜ?」の繰り返しはとても効果的です。
再発防止の重要度を測る
再発防止策の重要度は、工程や設備を根本から変えていくべきなのか、単純にヒューマンエラーに対する策を講じるべきなのかといった視点で考えていきます。若干抽象的ではありますが、大掛かりに改善が求められるものほど重要度が高いと考えておきましょう。また、危険性が伴うことに対する再発防止も重要度が高いです。
例えば、けが人が実際に出てしまった場合にはそれに対する再発防止の重要度は非常に高くなるでしょう。また、機械の故障などによって大量の不良品を製造してしまった場合も、重要度が高いと言えます。逆に、作業の中で10,000個製造するうちの5個を作業員の集中切れによって不良にしてしまった、という問題に対する再発防止策は上記のようなケースと比べて重要度が低いと言えます。
対策方法を講じる
原因究明と再発防止の重要度を測る工程を終えたら、実際に対策方法を講じていきます。この際、重要度の高い再発防止から取り組んでいきましょう。一度にいくつもの対策を実施するのは無理がありますし、従業員の大きな負担になりますので、重要度の高いものから取り組んでいくことが大切です。
労働災害を未然防止する監視カメラとAI画像解析の活用法とは?
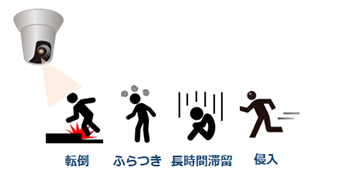
労働災害の未然防止・再発防止を実現するために、監視カメラやAI画像解析をどう活用するのか?をPDF資料に詳しくまとめました。
再発防止策の具体例
再発防止策を考えるにあたって、具体的にどのような手段を用いると良いのかをご紹介します。多くの作業ミスやトラブル、事故に関しては以下の3つを対策に組み込めば再発を防げるでしょう。
- マニュアル化する
- 機会最小を実行する
- RPAなどのシステムを導入する
共通して言えることは、なるべく人の手を加えすぎずに作業を実施するという点です。マニュアル化に関しては、作業員が独自の方法で作業をしないようにする手段で、機会最小やRPAは人が作業に関わる時間を最小限にすることでヒューマンエラーを防ぐ手段となります。
マニュアル化する
マニュアル化は再発を防止するうえで基本的な手段であり、正しく作成できれば高い効果が見込めます。マニュアルは様々な職場で活用することができます。製造業、建築業、サービス業などその分野でもマニュアルを作ることは可能です。
もちろん、作業員の技術力が問われるところは明文化するのが難しいですが、それ以外の部分はしっかりと明文化してしまえば従業員の作業を統一できます。作業が統一すれば、その分だけミスや事故が発生しにくいです。
逆にミスが発生してしまった場合は、マニュアルに従わなかった、マニュアルの精度が低かった、といった要因があると考えられます。
機会最小を実行する
機会最小とは、作業員が業務に関わる時間・機会を減らすことを指します。人の手による作業を最小にすることでヒューマンエラーを防ぐことが可能です。
機会最小をとる手段については、主に機械化が進められる業種に適していると言えます。例えば、製造業は製品を作る工程自体を機械化することによって人の手が加わる時間を減らすことが可能です。「服」は良い例で、昔は手作業で服を作っていましたが今となっては機械を使って全自動で服1枚を作れてしまいます。
このように機械に替えられるものがあれば、替えることでヒューマンエラーが発生する可能性を最小限に抑えられるでしょう。
RPAなどのシステムを導入する
RPAとは、ロボティックプロセスオートメーション(Robotic Process Automation)の略で、今まで人間が作業してきた高度な業務を自動化する技術のことです。RPAを利用したツール(RPAツール)を利用すれば、今まで自動化できなかった作業を自動化できる可能性があります。
自社の業務にRPAツールを導入できる部分があるのなら、導入することで自動化が図れるでしょう。自動化すれば作業工程に人の手が加わる機会が減るため、先述した機会最小にも繋がります。人の作業はムラがあるため再発に繋がりやすいですが、RPAツールの導入によって人の手を減らすことができれば再発防止に繋がるでしょう。
労働災害を未然防止する監視カメラとAI画像解析の活用法とは?
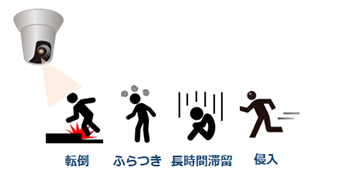
労働災害の未然防止・再発防止を実現するために、監視カメラやAI画像解析をどう活用するのか?をPDF資料に詳しくまとめました。
再発防止策を徹底するコツ
再発防止は策を立てるだけでは意味がありません。頭では分かっていても実際にやるとなると「意外にも現場では徹底できない」となることも珍しくありません。継続して決めた策を実施するためにも、以下のコツを把握して再発防止策を講じるようにしてみてください。
再発防止策を徹底するコツ
- 作業やルールをわかりやすくする
- 個人ではなく仕組みで防止する
- ダブルチェックを行う
とにかく、再発防止策について簡単に理解ができて、一人で完結させないように工夫することが大切です。全てを機械化するなら別ですが、人の手が少しでも加わるならその部分で想定外が起きないようにしなければいけません。上記3つのコツを再発防止策の中に組み込むことができれば、想定外が発生せずに策を徹底することができるでしょう。
作業やルールをわかりやすくする
作業やルールは作業員が分かりやすいようにすることが大切です。少しでも理解しにくい作業内容やルールになってしまうと、作業員が再発防止策を実際に取り組みにくくなる可能性があります。
また、「分かりやすい作業工程」や「分かりやすいルール」にすることは、作業員が継続的に取り組む上でも重要です。継続しやすいものというのは決まって簡単なことであるため、作業やルールが分かりにくくて複雑化していればその分継続がしにくくなります。
ですので、作業やルールは新入社員が来てもすぐに理解できるようにしておきましょう。
個人ではなく仕組みで防止する
再発防止策が継続的に取り組まれるかどうかを、作業員の力量に任せてはいけません。作業員も人ですから、その日の気分が乗らないといったことも必ずあるはずです。そういった時でもミスが再発しないようにするためには、作業工程などを仕組み化してしまうのが効果的と言えます。
仕組み化してしまえば、作業員が一つ一つのミスについて深く考えすぎる必要が無くなるため、安定した作業に期待できます。なるべくいろんなことを考えすぎずに作業に取り組めるような環境づくりに努めましょう。
ダブルチェックを行う
ダブルチェックとは、作業員の業務にミスが無いかを確認する作業のことです。ダブルチェックと言うものの、職場や製品によっては複数回確認作業をすることもあります。
ダブルチェックをすることによって、万が一作業員のミスがあったとしてもそれを社内で発見することができ、流出を防ぐことが可能です。流出が防げれば顧客にとっては再発にならないため、顧客への流出を防ぎたい場合には最適な方法と言えます。
また、ダブルチェックは複数の作業員が確認作業を行うため、初めの作業員が見逃した部分を他の作業者が気づける可能性が高いです。再発を徹底して防ぐという意味では、比較的精度の高い手法であると言えるでしょう。
労働災害を未然防止する監視カメラとAI画像解析の活用法とは?
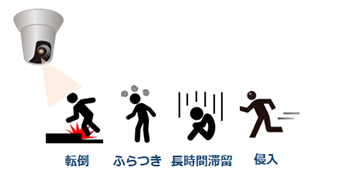
労働災害の未然防止・再発防止を実現するために、監視カメラやAI画像解析をどう活用するのか?をPDF資料に詳しくまとめました。
労働災害の再発防止策として活用できる「侵入検知サービス」と「危険行動検知サービス」
実際に労災が発生してしまった場合は、早急な再発防止が必要です。もし早急に対策を立てなければいけないにも関わらず、効果的な方法が思いつかないという場合には「侵入検知サービス」と「危険行動検知サービス」の2つのサービスをおすすめします。
それぞれのサービスの詳細は以下の通りです。
「侵入検知サービス」の概要
「侵入検知サービス」とは、特定のエリアへの不正侵入を検知した際に告知をするサービスのことです。危険を伴うエリアで労災が発生した場合に活用すると良いサービスになります。

カメラ内にインストールされたソフトウエアに対して予め進入禁止エリアを設定し、カメラで侵入を検知したら、メール通知、回転灯の点灯、製造装置の停止などの様々なアウトプットにより労災の発生を未然に防ぎます。工場内など、大きな機械を設置していて危険が伴うエリアがある場合には最適なサービスと言えるでしょう。
特に事故が起きてしまったエリアで「侵入検知サービス」を活用すると、再発防止策の1つになり得る可能性もあります。
「危険行動検知サービス」の概要
「危険行動検知サービス」とは、現場を撮影しているAIカメラが作業者の転倒やふらつきなどの危険行動をいち早く察知するサービスのことです。本人ですら想定できない体調不良によるふらつきなど、危険が伴う行動をとった場合にはカメラが検知して知らせてくれます。知らせる際は、担当者へのポップアップ通知や、回転灯の点灯などにより告知してくれます。
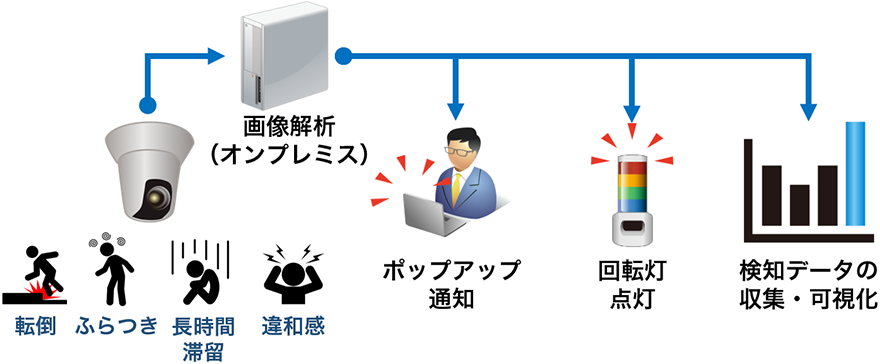
これにより、想定外の危険に対してもカバーできるため、思わぬ再発事故も未然に防げるでしょう。よく、危険を察知する活動でKY活動が取り上げられますが、あの活動は本人の意識があってこそ成り立ちます。作業員の無意識の中で発生する危険などには十分にカバーしきれませんが、そういった部分の危険を、「危険行動検知サービス」なら検知できます。
まとめ
再発防止とは、職場における作業ミスや品質上のトラブル、労働災害などを繰り返し発生させないように具体的な策をもって取り組むことです。作業ミスやトラブルの再発は顧客・取引先からの信用を損失することにも繋がりかねないため、徹底して再発防止に取り組まなければいけません。
再発防止を実現する方法として、職場内におけるルールの追加やマニュアル化などが挙げられますが、本記事では機会最小の実行やRPAツールの導入などなるべく人の手がかからないようにする方法をおすすめしています。例えば、危険行動検知サービスなど利用すれば、違和感をいち早く検知してミスやトラブルの防止に繋げられます。
利用できるツールは上手に活用して再発防止に繋げられれば、結果として顧客や取引先の信用を維持することに繋がるため、導入に対するコストは必要経費として考えることができるでしょう。
労働災害を未然防止する監視カメラとAI画像解析の活用法とは?
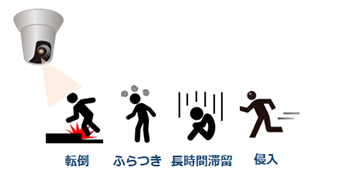
労働災害の未然防止・再発防止を実現するために、監視カメラやAI画像解析をどう活用するのか?をPDF資料に詳しくまとめました。