品質検査とは?
方法や検査項目・品質管理との違いなどをわかりやすく解説
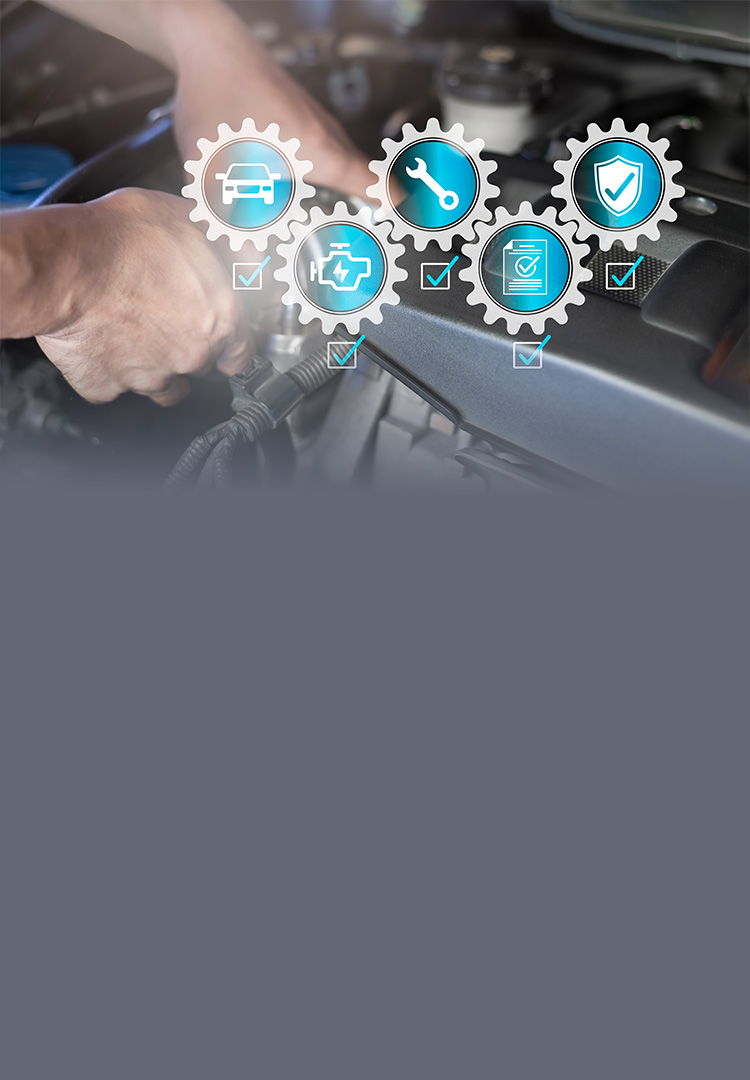
品質検査とは「製品が決められた規格・条件を満たしているか」を判断するために用いられる検査のことです。規格は製品ごとに異なり、外観を重視するものであればキズ等の検査が必要で、機能面を重視するものであれば寸法や構造等の検査が必要になります。
検査は顧客や消費者へ不良品を流出させないためにも重要な工程であるため、特に力を入れている企業も多いです。そのため、品質検査の重要性を理解したうえで、検査の精度を高める方法を知りたいと考えている人も多いのではないでしょうか。
本記事では、品質検査とは何か、その目的や種類、検査の自動化について解説します。
公開日:2025年4月14日
目次
-
品質検査とは
- 品質管理との違い
- 品質保証との違い
- 品質検査の目的
- 品質検査の方法
-
品質検査の種類
- 受入検査
- 工程検査
- 最終検査
- 出荷検査
-
目視検査の限界と自動化による可能性
- 自動化が見込める品質検査の項目
- 自動化が見込みづらい品質検査の項目
- カメラと画像解析による製品外観の品質検査自動化
- まとめ
品質検査とは
品質検査とは、その名の通り製品の品質を検査することで、一定の合格基準を満たしているかどうかを判断するために実施する工程です。品質検査の方法は製品に求められる企画・基準によって異なるため、全ての製品に対して共通した方法があるわけではありません。
例えば、製品には外観を重視するものと機能面を重視するものの2種類があります。外観を重視するものであればキズやゴミの挟み込みなどの検査、機能性を重視するものであれば寸法や耐久性などの検査を実施します。外観を重視しない製品に対して、過度な外観検査を実施すればムダな工程になるため、製品にあわせた検査が求められます。
品質管理との違い
品質管理とは、製品を一定の規格に基づいて検査し、品質が一定であることを保証するために管理することです。規格・基準を満たす品質を維持するだけでなく、少しでも効率よく高品質の製品を作るために管理することも品質管理になります。
例えば、目視で検査していた工程を設備導入によって自動化すれば、検査効率と精度が向上して品質の維持・向上が期待できます。つまり、品質管理を実施するうえで必要となるのが品質検査であり、品質管理の工程内に品質検査があります。
品質保証との違い
品質保証とは、製品が決められた水準以上の品質を維持しているかを確認し、顧客に納品後もその品質を保証する体系的な活動を指します。例えば、製品を検査した際の日報やデータチェックの詳細を残すことによる品質の担保、納品後のクレーム対応などの活動が挙げられます。
なお、品質保証と品質管理は似ている側面もありますが、それぞれ対象とする視点が異なります。品質保証は顧客に視点を向けており、品質管理は製造現場など作り手側に視点を向けています。そのため、品質保証はクレーム対応などが含まれますが、品質管理にはそのような業務は含まれません。
また、どちらの業務においても品質検査は含まれます。品質に関する工程のなかには、基本的に品質検査が組み込まれることを知っておきましょう。
品質検査の目的
品質検査の主な目的は品質を保証する点にあります。仮に品質検査を実施しなければ、顧客に不良品が流出する可能性が高まり、市場クレームや信用度の低下に繋がりかねません。逆に品質検査を実施して品質を保証すれば、顧客満足度の維持・向上、企業の信用度の向上が図れます。
また、顧客は製品に対して最低限の条件として一定の品質を求めています。顧客は品質の悪い製品は購入したがらないため、一定の品質が維持されていれば購入促進に繋がります。その結果、市場でシェアを拡大していければ企業の売上向上にも期待できます。
品質検査の方法
品質検査の方法は主に外観検査と機能検査の2種類があります。それぞれの違いは以下の表の通りです。
検査方法 | |
---|---|
外観検査 | 製品の体裁部分におけるキズや汚れ、その他外観を損なう不良が発生していないかを検査する。主に良品サンプルとの比較や、限度見本と呼ばれる不良サンプルとの比較といった方法を採用しているケースが多い。 |
機能検査 | 機能性に問題がないかを判断するため、寸法検査や動作チェックなどを行う。自動車の走行テストや工業系機械の試運転なども機能検査に該当。 |
どちらの検査方法を採用するかは、製品の種類によって異なります。例えば、車の内部に組み込まれ、顧客の目に付かないような部品の場合、外観検査をする必要がありません。不要であるにも関わらず外観検査を取り入れた場合、その検査にかかるコストは企業にとってムダな支出となります。
品質検査の種類
品質検査の種類は以下の4種類があります。
検査する内容 | |
---|---|
受入検査 | 受入の際に行なう検査。仕入れた製品が良品かどうかを判断するために用いられる。 |
工程検査 | 各工程内で実施する検査。1つの製品を作り上げるために、部品の製造や組立の工程が複数ある場合は、全ての工程で検査を導入するケースもある。ただし、全ての工程に工程検査を組み込むとそのコストは大きくなってしまい負担が増加する。 |
最終検査 | 製品が完成した際にその製品の全てを確認する検査。外観、動作など顧客が利用するにあたって不具合が無いかを確認する目的で行われる。 |
出荷検査 | 出荷が決まった際、出荷前に行なう検査。製品が問題なく使用できるかを検査する工程であり、最終検査ほど念入りに実施されることはほぼ無い。数ヶ月保管していた在庫品を出荷する際などに組み込まれやすい。 |
品質検査がある全ての企業で、これら検査が必ず実施されるわけではありません。部品や原料の仕入れがない場合は受入検査がありませんし、最終検査と出荷検査をまとめて実施しているケースもあります。自社が取り扱う製品によってどの品質検査が必要かを判断しなければなりません。
受入検査
受入検査とは、その名の通り「受入」の工程時に実施する検査です。受入が発生する状況は様々で、製造に必要な原料を仕入れるケースや外部の企業に発注した部品を仕入れるケースなどがあります。
自社の製造時に必要な原料や部品を仕入れる際、受入検査によって正常品が仕入れられているかどうかの判断が可能です。仮に受入検査をしなかった場合、不具合品が混入していても気づかず、そのまま利用して不良品を生産してしまう可能性があります。そのような損失を防ぐためにも、受入検査は重要な検査工程の一つです。
工程検査
工程検査とは各工程で実施する検査を指します。各工程で検査を取り入れることで、早い段階で不具合の発生を検出可能です。工程の種類や数は製品によって異なるため、工程数が多い場合には全てに検査を組み込むとその分だけコストがかかります。
そのため、工程検査を取り入れる場合は不具合が発生すると重大な損失になる工程を優先しつつ、必要に応じて実施するかどうか検討しなければなりません。
例えば、外部から仕入れるものに関しては自社で管理しているわけではないため、検査したほうが想定外の不具合に対処しやすいです。一方で、自社で製造したものを次工程に回す場合(製造工程→組み立て工程など)、自社の管理基準に基づいて製品を移しているため工程検査の重要性は低くなります。
最終検査
最終検査とは、製品が市場に出回る前に実施する検査で、主にメーカーで取り組まれることが多いです。市場に出せるだけの品質基準を満たしているのかを検査し、その検査で合格した製品が市場へ出ていきます。
市場へ出ていく製品はその企業の看板を背負って出ていくため、不具合品などが出回ればそれだけで自社のブランドに傷がつく可能性があります。そのため最終検査では、安全面・外観面など広い範囲に対して検査項目を設けるケースが多く、その重要性は特に高いです。
出荷検査
出荷検査とは、その名の通り出荷する際に実施する検査です。最終検査を終えている製品を出荷前に検査するため、主に動作不具合や梱包時に発生したひどいキズなどが無いかを検査します。例えば冷蔵庫の場合、電源を入れて規格通りに作動するか、正常に温度が下がるかなどが検査対象になります。
つまり出荷検査は、顧客の手元に製品が届き、問題なく利用できるかどうかを確認する検査です。
目視検査の限界と自動化による可能性
外観を検査する方法の一つに目視検査があります。目視検査は人の視力や見え方、光の当たり方などによって不良を検出できるかどうかが変わるため、人によって検査精度にばらつきが出やすいです。そのため、ばらつきを減らすために以下のような方法で不良の見逃しを防ぐこともあります。
- 全員が同じ環境で検査する(照度の統一、目視する角度の統一、メガネなどを使用して一定の視力を確保できるように統一 など)
- 製品ごとに決められた人材を検査に充てる(同じ人が検査することで検査基準が統一される)
- 画像検査など機械による検査でヒューマンエラーを防ぐ
ばらつきが最小限になるような仕組みを作ったとしても、少なからず検査精度に差は発生します。そのため、最終的には検査員の技量に不良が流出するかどうかが左右されてしまいます。検査員の技量が十分ではない企業の場合、不良の流出に頭を悩ませているケースも多いのではないでしょうか。
その点、機械を導入して検査の自動化を図れば目視による検査のばらつきや検査業務の属人化を防げます。検査機械の性能が向上してきていることもあり、製造業の企業によっては検査機械による検査の自動化を進めているケースも少なくなりません。
また、検査機械を導入すれば設備導入費はかかるものの、人件費の削減や業務効率化にも繋がるため、結果として企業の利益向上にも期待できます。
自動化が見込める品質検査の項目
検査機械を導入して検査の自動化を図る場合、どのような検査を自動化できるのか知っておく必要があります。検査機械で検査する際に検出できる項目は以下の通りです。
- 寸法:登録された寸法データをもとに対象品の寸法を測定。公差外となった場合は不良品として検出。
- 形状:登録した正規品データ(図面など)と比較した際の形状違い(変形や欠損など)の検出。
- 色:登録された製品画像と比較して、対象品が異なる場合に不良として検出。色ムラや色調違い、変色などを検出可能。
- 構造:製品同士を組み立てた後のズレなどを検出。
外観に関する検査内容であれば、これらの項目で一通りの不良検出が可能です。ただし機能や耐久性などは検査できないため、検査項目から対応できる範囲を把握したうえで自動化を進めるべきか検討する必要があります。
自動化が見込みづらい品質検査の項目
検査装置をもってしても自動化が見込みづらいケースもあります。例えば、形状が複雑で且つ全面の検査をしなければいけない場合、カメラで写せない範囲の検査はできません。そのため、製造ラインの中で製品を反転させる機械などの導入が必要になるケースもあり、このようなケースだとさらに設備導入コストがかかります。
コストを抑えたい場合には、検査機械で検査できる工程と人の目視による検査を分担して工程を組むのも一つの方法です。また、昨今においてはAIの性能が上がってきていることもあり、自動化した際の検査精度・スピードはかなり速くなってきています。
機械に全てを委ねるのではなく、社内で出来る工程と自動化できる工程を明確に区別したうえで、検査工程を組み立てることを推奨します。
カメラと画像解析による製品外観の品質検査自動化
品質検査の中でも製品の外観検査については、下記のようにカメラと画像解析システムを活用することで、検査を自動化することができます。主に、製造物(製品)に貼られているラベルやバーコード、QRコードの検査、製品外観の汚れ、欠け、バリ、変形などの検査が可能です。
さらに、検査結果を帳票に自動連携することもでき、見逃し対策や記入漏れ、転記ミス、集計ミスを削減することができます。
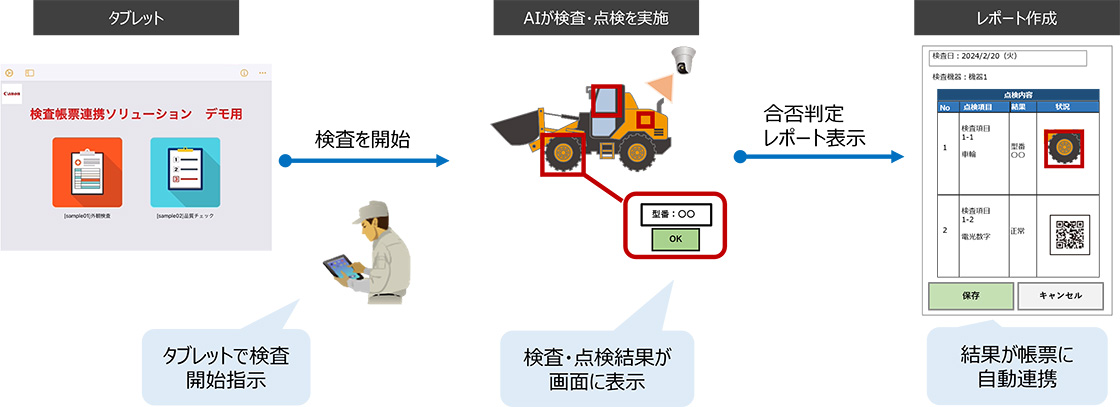
まとめ
品質検査では、自社(もしくはメーカー)が定める規格・基準に基づいて製品の良し悪しを検査します。検査の種類は主に受入検査・工程検査・最終検査・出荷検査があり、それらの検査工程の中で外観検査や機能検査といった方法を使い分けます。
機能検査は寸法測定や動作チェックなど数値的な判断をするケースが多いですが、一方で外観検査は人の目による検査を実施するため検査員によって検査結果にばらつきが出やすいです。そのため、検査環境を統一する、検査機械を導入するなど、ばらつきを抑える方法を駆使しないと不良を流出してしまう可能性が高まります。
なお、検査機械はAIの性能が向上してきていることもあり、精度・スピードの両方の質が向上しています。人の目で確認する工程と検査機械によって自動化を図る工程を明確にし、検査の自動化を進められれば、企業の利益向上などが期待できます。