外観検査とは?
目視検査の不良見逃しを減らすコツやAIによる効率化の可能性を解説
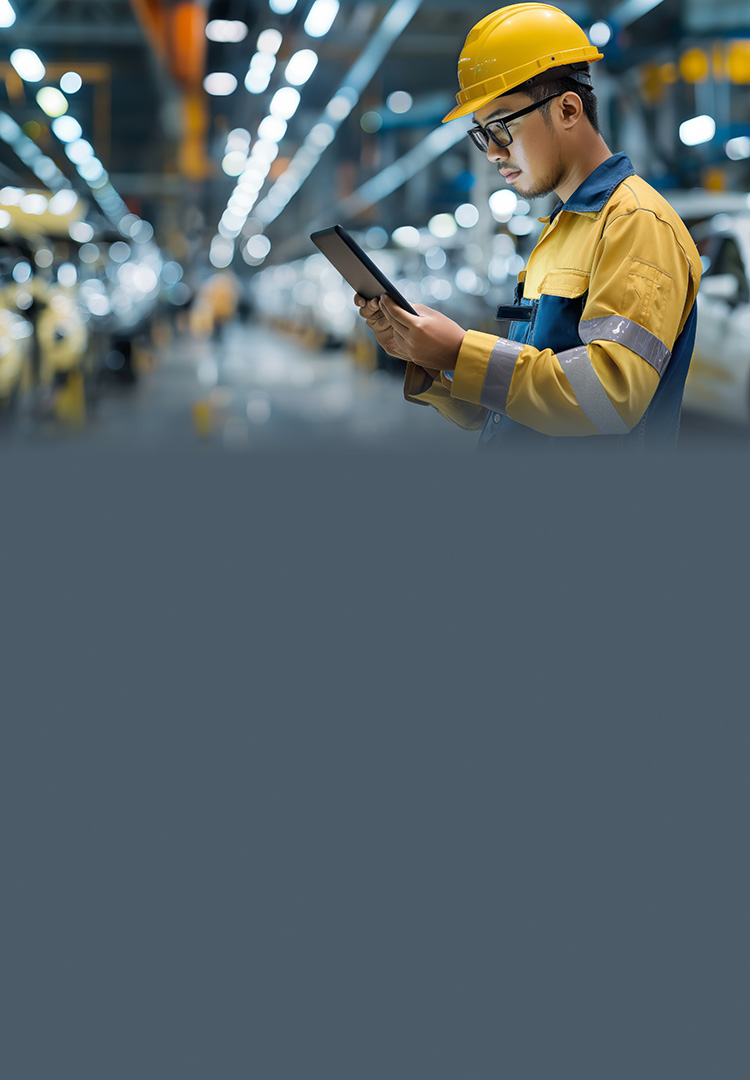
外観検査とは、部品・製品の外観部分における品質に問題がないかを確認する検査です。主に目視や画像検査などで実施し、キズや汚れ、ラベルやQRコードなどのズレ・かすれ等の不良品を検出します。特に目視においては、作業員の能力によって検出レベルにムラが発生しやすいため、不良流出の防止対策に頭を悩ませている人も多いのではないでしょうか。
本記事では、外観検査の項目や具体的な方法、見逃しを減らすコツを解説します。外観検査はライン上の様々な工程で実施されるため、その知識を深めることで製造工程全体の質を上げるきっかけにもなるでしょう。
公開日:2025年4月14日
目次
- 外観検査とは
-
外観検査の主な項目
- 製品の形状や構造
- 製品の表面
- 製品の仕上がり
-
外観検査の方法
- 目視検査
- 外観検査装置を使用した検査
- 外観検査が難しい理由
-
外観検査の不良見逃しを減らすコツ
- 検査員の環境整備
- 検査時間を短くする
- 外観検査基準書を更新する
- カメラを利用した画像解析による検査工程の追加
- AIなど機械による自動化
- まとめ
外観検査とは
外観検査とは、部品・製品における外観部分に不具合等がないかをチェックする検査です。主に製品の表面・体裁部分を検査し、以下のような不具合が発生していないかを検査します。
- キズ
- 汚れ
- 異物
- バリ
- ラベル・QRコード等の傾き
- ラベル・QRコードの読み取り
- 欠け・打痕
- 変形 など
その他にも、製品や製造方法によって発生する独自の不具合が存在します。実際に検査項目を決定する場合は、製品の特徴を理解していないと作れないため、製造方法や製品の理解度は深めておかなければいけません。
なお、外観検査において上記のような不良項目が少しでも発生していたら、必ずNGとなるわけではありません。製品ごとに品質の基準は異なるため、用途などに合わせた検査が求められます。
外観検査や目視検査の効率化・ミス防止に関するPDF資料
外観検査の主な項目
外観検査を実施するにあたり、どの項目を検査するのかを押さえておかないと正しい検査が行えません。主な項目は大きく分けて以下の3つがあります。
確認する内容 | 発生する問題の例 | |
---|---|---|
外観検査製品の形状や構造 | 図面通りの製品が作られているか。他製品との組立がある場合には、問題なく組立を実行できるか。 |
|
製品の表面 | 表面にキズや汚れが無いか。表面の見た目は標準規格品と同等の仕上がりになっているか。製品ラベルやラベル内のQRコードの確認 |
|
製品の仕上がり | 製品に仕上げを要する場合、仕上げ部分の処理は問題ないか。 |
|
外観検査では体裁面を上記の項目と照らし合わせて、目視で検査します。一般的に以下で示す5つの「みる」を意識して検査することで、不具合の発生を防ぐことに繋がります。
- 見る:目視検査で合否判断を実施
- 観る:不良情報から発生原因や変化点を調査
- 視る:不良情報と現場の状況から発生原因を調査
- 診る:不良が発生する原因に対して、改善するための方法を検討
- 看る:改善方法を実施して、根本的な原因を解決
ただ検査をするのではなく、原因の追究なども検査の一環として「みる」ことで、根本的な原因の解決にも期待できます。不良内容を正確に把握できなければ、改善には繋げられないため、細かな不具合でも検出できるかどうかが重要です。
製品の形状や構造
製品の形状や構造の項目においては、製品の規格に基づいた外観となっているかどうかを検査します。主に図面に基づいた製品となっているかを検査するため、形状や色味、意匠などが検査項目になります。詳細は以下の表の通りです。
形状 | 欠損や変形、形状違いなど |
---|---|
構造 | 組立・勘合における位置ずれ・差異など |
寸法 | 図面寸法との違いなど |
色 | 変色や色ムラ、色調の違いなど |
意匠・印刷 | 図面で指定された意匠や印刷との違い、図面通りにラベル等が貼られているかなど |
量産する場合には、図面と照らし合わせるよりも標準品となる製品と見比べて検査する方が効率が良いです。標準品と比べることで形状違いだけでなく、色味などの違いも明確に検出しやすくなります。
また、製品への印刷が後加工である場合には、外観検査装置を使用して検査するのもおすすめです。これにより、印刷位置の精度だけでなく、にじみやインクのカケ・ピンホールといった不具合も検出できます。
製品の表面
製品の表面検査では、外観がきれいに作られているかどうかを検査します。前項の形状や構造では主に「機能面」を重視した検査であるのに対して、表面の検査では主に「見栄え」を重視して検査します。
キズ | 製品表面のキズ、擦り傷 |
---|---|
付着物 | ほこりや異物、指紋(皮脂)など |
感触・見栄え | 凹凸やシワ、ツヤ、劣化、ラベルの汚れなど |
製品特有の不具合 | プラスチックであれば、成形時に発生するガスムラや空気を巻き込んだ銀線(シルバー)など |
製品ラベル・QRコード | 製品に貼り付けられているラベルの向き、汚れや、QRコードの読み取り確認 |
見栄えを重視した検査となるため、人目に付きやすい部分の製品に対して実施されるケースが多いです。主に目視での検査が多く、光の当たり方の加減で顕著に見える不具合などを検出します。製品によっては0.01mm²単位での検査が求められるケースもあり、他2つの検査項目と比べても特に難易度が高い検査であるといえます。
製品の仕上がり
製品の仕上がり検査は、製品に対して「仕上げ・加工」がある場合に行なう検査です。主に人の手による仕上げにミスが無いかを確認する検査であり、不具合の傾向が掴みにくい傾向にあります。
仕上げのクオリティ | バリや仕上げ・加工跡など |
---|---|
内職作業のクオリティ | ラベル貼りなどによって発生するラベルの傾き、シールのしわの発生など |
仕上げの内容は製品によって異なるため、どのような検査を実施するべきか、製品ごとに区別する必要があります。例えば、金属製品の場合、研磨加工があったとすると光沢の度合いが検査対象になります。プラスチック製品の場合は、プラモデルのように不要な部分をニッパーで仕上げする工程があれば、その仕上げ部分の切り口のきれいさが検査対象になります。
また、ラベルなどを貼り付ける工程がある場合には貼り付け作業で発生する不具合の検査も必須です。貼り方が下手でしわになってしまう、何かしらの汚れが付いて読み取りが難しい可能性がある、といった不良の発生が考えられます。
外観検査の方法
外観検査の方法は主に以下の2つがあります。
検査方法 | |
---|---|
目視検査 | その名の通り「目」で検査をする方法。光に表面を当てて検査する方法や、光を透かして検査する方法などがある。 |
外観検査装置を使用した検査 | 機械を使って自動で検査をしていく方法。ライン上に組み込んで高速で検査するケースもあれば、一つずつ検出して寸法や外観の検査をするケースもある。 |
多くの中小企業では目視検査にて製品の外観検査を実施しているケースが多いです。その理由には、設備導入コストを工面できないなどの理由もありますが、検査しなければいけないポイントが多いなどの理由もあります。
外観検査装置の場合、カメラで検査するためカメラに映らない範囲は検査できません。そのため、1度の検査で複数の面を検査しなければいけない場合には外観検査装置は適していない可能性があります。一方で目視検査なら、人の手で製品を持って検査するため多面にわたる検査が必要だとしても、その工程内で検査を完結させることができます。
目視検査
目視検査はその名の通り、人の目を使って製品の外観を検査する方法です。実際に製品を手に取り、検査箇所が見えやすい角度で検査して不具合を検出します。不具合を検出するには部屋の照度や見る角度が重要で、人それぞれ見方が異なると不良の検出精度は低下します。
人の検査能力に精度が左右される点はデメリットですが、多面的に検査ができる点や設備導入をせずに低コストで検査できる点は目視検査のメリットです。また、目視検査の場合はイレギュラーな不良(機械の場合は設定したものしか検出しない)の検出にも適しています。
目視検査には以下の4種類が存在し、それぞれメリット・デメリットがあります。どの方法を採用するかは、製品の特徴や用途に合わせて判断しましょう。
メリット | デメリット | |
---|---|---|
インライン検査 |
|
|
オフライン検査 |
|
|
全数検査 |
|
|
抜き取り検査 |
|
|
外観検査や目視検査の効率化・ミス防止に関するPDF資料
インライン検査
インライン検査とは、生産ラインの中に組み込まれる検査のことです。ライン上で検査するため、製造中の製品をリアルタイムで検査できます。リアルタイムで検査することによって、急な不具合が発生したとしても最短で製造を中断できるため、不具合発生時のロスを最小限に抑えることが可能です。
また自身のペースで検査するのではなく、生産ライン上で流れてくる製品に合わせて検査をしなければいけないため、検査のペースが過度に遅くなりすぎないメリットがあります。
但し一方で、ライン上に流れてくる製品すべてを検査しなければいけないため、検査員のキャパシティを超えてしまう懸念もあるでしょう。仮にキャパシティを超えてしまうと、不良品の見逃しが発生する可能性があるため、管理側は検査員の能力に合わせた工程を組むなどの工夫があります。
オフライン検査
オフライン検査とは、インライン検査とは対照的に生産ラインから外れて行う検査のことです。インライン検査の場合はライン上で流れてくる製品のペースに合わせて検査をしていましたが、オフライン検査の場合はライン外で検査するため製品一つひとつに時間をかけて検査できます。
ただし、時間をかけすぎると逆に検査コストが増加してしまうため注意しなければいけません。管理者は検査員一人ひとりの検査ペースを実績データから把握し、求めるペースでの検査を実行できているか確認する必要があります。
また、オフライン検査は生産ラインの流れに作業員が追われずに済むため、検査員を育てる場としても有効です。
全数検査
全数検査とは、その名の通りすべての製品を検査することです。全数検査をすることによって、不良が流出してしまう可能性を限りなくゼロに近づけられます。「限りなくゼロ」と表現したのは、目視での検査である以上、見逃す可能性はゼロではないためです。
人の手で作業する以上、ミスが発生する可能性は必ずあるため、工程を検討する側はミスが発生しないような工夫が求められます。例えば、画像検査機と目視検査を合わせて利用する、全数検査かつダブルチェックを実施して検出精度を上げる、といった工夫が挙げられます。
ただし、時間をかけて検査すればするほどかかるコストは膨大になるため、コスト面において無理のない方法が何かを追求する必要があります。例えば、全数検査はするが特定の箇所の検査は不要、などのようにムダな検査工程を減らすのも一つの方法です。
抜き取り検査
抜き取り検査とは、全数検査とは違って決められた数量を取り出して検査する方法です。いくつ抜き取るかは企業ごとに決めるのが一般的で、「1,000個で1ロットを構成している場合は、10%の100個を抜き取り検査する」といったようにルールを決めて実施します。
製品を外注しており、それが納品された際に実施されることが多いです。そのため、抜き取り検査をして不良が検出された場合は「ロットアウト」となって、外注へ返品することもあります。受け入れした製品・部品に不良が多発すると、自社での製造に悪影響を及ぼす可能性もあるため、そういった事態を防ぐために抜き取り検査は実施されます。
外観検査装置を使用した検査
外観検査装置とは、カメラや画像センサー、画像処理システムなどを活用して行う検査です。人の目ではなく機械に頼るため、検査精度にムラが発生しません。そのため安定した品質での製品供給が可能となり、品質を保証しやすくなるメリットがあります。
また、ライン上に導入すれば高速での検査もできるため、大量生産が求められる製品を取り扱う場合に適しています。人件費も最小限で抑えられるため、検査コストは大幅に抑えられます。
さらに、外観検査装置にはAIが組み込まれているケースもあり、AIを活用することによって不良の傾向を学習させるといった高度な設定も可能です。人による検査だけではなく、機械の導入による検査工程の構築も効率化につながるでしょう。
ただし、設備を導入するコストはかかってしまうため、ゼロから設備を導入する場合にはある程度の資金が必要です。資金繰りに不安を抱えている人は、ものづくり補助金などの補助金の利用を検討してみるのもおすすめです。
外観検査が難しい理由
一般的に外観検査は以下の理由によって難しい作業と考えられています。
- 製品によっては0.01mm²単位での検査が求められる
- 不良発生率が少ないものを検査する場合は、検出すること自体が困難
- 検査になれている人とそうでない人で明らかにスキルの差が出やすい
- 長時間にわたって目視検査をすること自体が体力的にラクではない
以上のように様々な理由が挙げられますが、特に検出する不良のサイズが小さい場合や、ほとんど不良が発生しない製品の検査をする場合には検査員の質が重要視されやすいです。
例えば、面積が0.01mm²の異物を検出しようとすると、かなり目を凝らさなければいけませんし、見方次第では全く検出できない可能性もあります。さらには、視力が悪いとどれだけ目を凝らしても見えないといったこともあるでしょう。
また、不良発生率が少ない製品を全数検査しなければいけない場合、1,000個の製品に10個不良があるかどうかの検査をしなければいけないこともあるため、その労力はかなりのものです。要領を得るまでに時間がかかりやすい作業でもあるため、外観検査は「難しい」とされています。
外観検査や目視検査の効率化・ミス防止に関するPDF資料
外観検査の不良見逃しを減らすコツ
前項で触れたように外観検査は決して簡単な作業ではありません。本来不良品を流出させないために行なう工程であるにもかかわらず、検査員の熟練度によっては品質を保証することが危ぶまれます。そのため、以下のコツを押さえて見逃す可能性を少しでも抑えることが重要です。
外観検査の不良見逃しを減らすコツ
- 検査員の環境整備
- 検査時間を短くする
- 外観検査基準を更新する
- カメラを利用した画像解析による検査工程の追加
- AIなど機械による自動化
安定した検査を実現するためには、検査員の作業環境を整えるのも重要です。気が散ってしまうような環境下で検査をしていると、必ず気のゆるみが発生して不良の流出に繋がります。また、作業工程の仕組みを改善するのも重要で、検査時間を短くして集中しやすくする、基準を決めて判断効率を上げるといったものも効果的です。
機械化による自動化は、品質を安定させるうえで最も効果的な方法といえます。ただし、設備導入コストがかかるだけでなく、機械で対応できない部分もあるため、機械の仕組み等をよく理解したうえで導入を検討しましょう。
検査員の環境整備
検査員の環境整備によって、検査員が集中しやすい環境下で検査にあたれるようになります。数十個の検査ならまだしも、1日で1,000個~2,000個といった量を検査しなければいけない場合は、長時間にわたって集中力を保つ必要があります。そのため、集中するための環境整備は欠かせないポイントです。
環境が悪ければ、別のことに気が散ってしまって見逃しが発生する事態になりかねません。ましてや不良率の低い製品を検査している場合は、一瞬油断したタイミングで不良を見逃す可能性もあるため、気を抜くことが許されません。
そこで、集中力を維持するためには、以下の環境整備の方法を実践してみましょう。
- 照明設備を一定にする
- 検査基準を明確にしたマニュアルの策定
- 検査方法・工程をマニュアル化して作業方法を統一
- 外観検査装置の導入
- 適切な空調管理
「現場環境を揃えること」「検査方法を揃えること」「設備導入によって検査員の負担を軽減」といった整備方法があります。設備は分かりやすい環境整備の一つですが、検査工程の標準化など仕組みを作って働きやすい環境を作るのも環境整備に該当します。
検査時間を短くする
一つの製品に充てる検査時間を短くすれば、メリハリがつきやすくなるため検査員の集中力が持続しやすいです。検査作業は同じ作業を延々と続ける過酷な作業であるため、作業時間が長くなるほど検査員の負担は大きくなります。
そのため1つの製品にかける検査時間を短くできれば、1つの製品の検査が完了して、次の製品を検査するまでの間にわずかな時間を作ることができます。どれだけ短くてもわずかな隙間時間を作れるように工夫すれば、検査員の負担を減らして集中力を持続させる要因となります。
また、定期的に休憩時間を設けて作業時間を短く分けるのもおすすめです。「1時間作業→5分休憩」といった仕組みにするだけでも、集中力を維持させる要因となります。ただし、生産ラインに組み込まれるインライン検査では休憩時間を調整するのが難しいため、事業部全体を巻き込んだ話し合いが必要です。
外観検査基準書を更新する
外観検査基準書とは、対象製品の外観基準を明記している書面です。具体的には以下の内容が記載されています。
- 不良の内容
- 具体的な不良発生箇所
- 不良と判断される判断基準(異物の大きさ限度など)
- 判断ができない不具合が発生した際の報告方法
- 過去の不具合発生履歴 など
企業ごとに記載内容に差はありますが、作業員が書面を見て検査の判断を一人でできるような書面を作ることが重要です。ときには写真を載せるなどして、分かりやすく記載するのも大切で、現場とすり合わせをしながら作りましょう。
また、不良が流出した際や今までに検出したことの無い不良が発生した際には、必ず書面の更新をしてください。
カメラを利用した画像解析による検査工程の追加
カメラで製品の検査部分を撮影し、撮影したデータを画像解析ソフトに読み込ませることで、基準外の製品を設定値に基づいて検出できます。人の目では検出しづらい細かな不良も検出できるため、検査精度をより高めることが可能です。
また、画像解析ソフトと別システムを連携させれば、検査帳票(検査成績表など)に自動で数値を入れるといった連携も可能になるため、帳票作成の手間を削減できます。その結果、無駄な作業が減って業務の効率化の効果も得られます。
画像解析による検査は半自動的な工程となりますが、AI等を組み込めば全自動での検査も可能です。AIを利用した全自動化は次項で解説するため、あわせて参考にしてみてください。
AIなど機械による自動化
AIに良品や不良品の画像データを読み込ませて学習させることによって、検査を自動化できます。目視検査ではヒューマンエラーを防ぐことはかなり難しいため、自動化によって機械的に検査をした方が流出を防ぎやすいです。導入すれば検査員の休憩等も考える必要がなくなりますし、検査しやすい環境を整備する必要もありません。
なお、AIなどによって検査を自動化した場合、設定したルールベースでの判断をさせなければいけないため、判断基準の入力等は正確に行わなければいけません。設定が難しいため、入力内容もルール化しておかないと、結果的に機械操作が属人化する可能性もあるため注意が必要です。
とはいえ、操作に専門知識が必要というわけではないため、設備導入時に使用ルールを明確化しておけば円滑な運用が可能です。
まとめ
外観検査とは、部品・製品における外観部分に不具合等がないかをチェックする検査です。主に人の目に触れる部分を検査するため、わずかな見逃しが消費者からのクレームに繋がる可能性があります。そのため、検査員の質はどの企業でも悩みの種となりやすく、不良を流出させないための方法を模索し続けている企業は多いです。
なお、外観検査装置を導入して機械に検査を任せるのもおすすめですが、目視検査でないと検出できない不良もあるため一概に機械導入がベストとは限りません。製品の規格や用途を理解したうえで検査内容は明確にしなければいけないため、必要に応じて目視検査と機械による検査を使い分けましょう。