トラックバースとは? トラックヤードとの違いや荷待ち時間を解消する方法を解説

トラックバースとは、荷物を積み下ろしするためにトラックを倉庫に接車しておくスペースのことです。トラックバースの効率的な運用や荷待ち時間短縮のためのシステム導入によって、スムーズな入出荷オペレーションと物流コストの削減を実現できます。
運送業界における人材不足は深刻な状態であり、トラックバースやバース予約システムの関係性などを押さえておくことで、ムダを排除した効率的な運送業務へと繋げられるでしょう。
本記事では、トラックバースやその種類、発生する荷待ち時間の問題などを解説します。より効率的な物流を実現したいとお考えのご担当者様は、ぜひ参考にしてください。
目次
-
トラックバースとは
- トラックヤードとの違い
- プラットフォームとの違い
-
トラックバースの種類
- 高床式倉庫
- 低床式倉庫
- トラックバースで発生する問題
-
トラックバースで荷待ち時間が発生する原因
- 到着時間が管理しづらい
- 倉庫内作業との非効率な受け渡し
- 入荷と出荷を同時に行っている
- 人材不足
- バース周辺のレイアウト
-
トラックバースの荷待ち時間を解消する方法
- バース予約システム
- 倉庫管理システム(WMS)
- 在庫管理システム
- EDIシステム
- 検品システム
- まとめ
トラックバースとは
トラックバースとは、荷物を積み下ろしするためにトラックを倉庫に接車しておくスペースであり、物流センターや物流施設の倉庫などに設置されています。
船舶が入港した際に停泊して貨物の荷下ろしをする場所である岸をバース(Berth)と呼びます。そして、トラックの荷物の積み下ろしの場所も、そのままバースが使われるようになりました。
トラックバースのことを略して「バース」と呼ぶこともあります。
トラックバースでの荷待ち時間を解消する方法とは?
- 到着時間が管理しづらい
- 荷主側の準備が間に合っていない
- 入荷と出荷を同時に行っている
- 複数のトラックが同時に来場する
トラックバース問題の解消のヒントをPDF資料でご紹介
-
トラックバース予約システムとは?基礎と選び方、導入手順とおすすめ製品
トラックドライバーの長時間労働の要因となるトラックバース問題を解決する方法
トラックヤードとの違い
トラックヤードとは、トラック(貨物自動車)や海上コンテナなどから荷物の積み替えを行う敷地全体を指す言葉です。トラックヤードには、トラックバースの他にもさまざまな設備が含まれています。
トラックバースが荷物の積み下ろしに特化した場所であるのに対し、トラックヤードは他の運輸方法に移し替える中継地となる、より広範囲の場所を指します。
プラットフォームとの違い
プラットフォームとは、トラックや運搬用トレーラーなどの貨物の積み下ろしや運搬・入出庫・ピッキングなどといった荷役を行うための台状の設備のことです。倉庫の床面を車両の荷台と同じ高さにすることで、フォークリフトなどを使わずに作業を直接人の手で行える構造になっています。
トラックバースが荷物の積み下ろしの際に駐停車する場所を指すのに対して、プラットフォームは荷物の積み下ろし場所の設備そのもののことを指します。
また、トラックバースの種類の一つである高床式倉庫は、プラットフォーム型の倉庫とも呼ばれます。トラックバースの種類については、後述します。
トラックバースの種類
トラックバースには、高床式と低床式の2種類があります。それぞれの特徴やメリット・デメリットは以下の表の通りです。
高床式倉庫 | 低床式倉庫 | |
---|---|---|
特徴 | トラックの荷台と同じ高さに床面がある | 地面と同じ高さに床面がある |
メリット |
|
|
デメリット |
|
|
高床式倉庫は「トラックの荷台と同じ高さに床面がある」、低床式倉庫は「地面と同じ高さに床面がある」ところが、大きな違いであり特徴です。
それぞれ、トラックなどの車両と倉庫の出入り口が接する場所の構造や、荷物を管理しておく場所の構造がまったく異なります。そのため、積み下ろしや荷物の運搬・管理といった面でのメリット・デメリットに、大きな差が発生するでしょう。
高床式倉庫と低床式倉庫の概要やくわしいメリット・デメリットについては次項で解説します。
高床式倉庫
高床式(たかゆかしき)倉庫とは、床面がトラックの荷台と同じ高さに設計された倉庫です。トラックバースに接続された床面と倉庫内部の床面が同じ高さに統一されているため、トラックの荷台から商品の搬入出作業がスムーズに行えます。
また、高床式は、地面から高い位置にあるため、構造的にホコリの堆積や湿気を避けやすく、商品の傷みを防ぐという衛生的な観点においても優れています。浸水のリスクも少ないため、台風や大雨などが多い地域においては、より安心して商品管理ができる点もメリットとなり得るでしょう。
一方で、出入り口が高い場所にあるため、トラックやフォークリフトなどの重機はそのまま倉庫内に入れません。床を底上げしなければならないことから建築費も高い傾向にあり、保管料が高く設定されている場合もあります。
低床式倉庫
低床式(ていしょうしき)倉庫とは、床面が地面と同じ高さに設計された倉庫です。トラックバースに接続された床面が地面と同じ高さになっているため、トラックやフォークリフトなどの重機が自由に出入りできます。
倉庫内へ車両ごとに入って荷物の積み下ろしをするため、雨や雪など天候不良の際でも商品を濡らすことなく作業ができます。また、建築の際には床あげが必要ないため、高床式と比較して建築費用を安く抑えやすいです。
ただし、低床式倉庫では倉庫内部の床面が低くなっている分、浸水被害のリスクが高くなる傾向にあります。倉庫内で取り扱う商品や立地条件などを十分に検討する必要があるでしょう。
トラックバースでの荷待ち時間を解消する方法とは?
- 到着時間が管理しづらい
- 荷主側の準備が間に合っていない
- 入荷と出荷を同時に行っている
- 複数のトラックが同時に来場する
トラックバース問題の解消のヒントをPDF資料でご紹介
-
トラックバース予約システムとは?基礎と選び方、導入手順とおすすめ製品
トラックドライバーの長時間労働の要因となるトラックバース問題を解決する方法
トラックバースで発生する問題
国土交通省が実施した「トラック輸送状況の実態調査(令和3年1月~3月)」によると、ドライバーの拘束時間は荷待ち時間に大きく影響を受けており、その長さは平均1.34時間であると判明しました(Fig1)。これは2023年6月に経済産業省、農林水産省、国土交通省が連盟で公表しているガイドラインの最終目標である1時間を大きく超過しています。
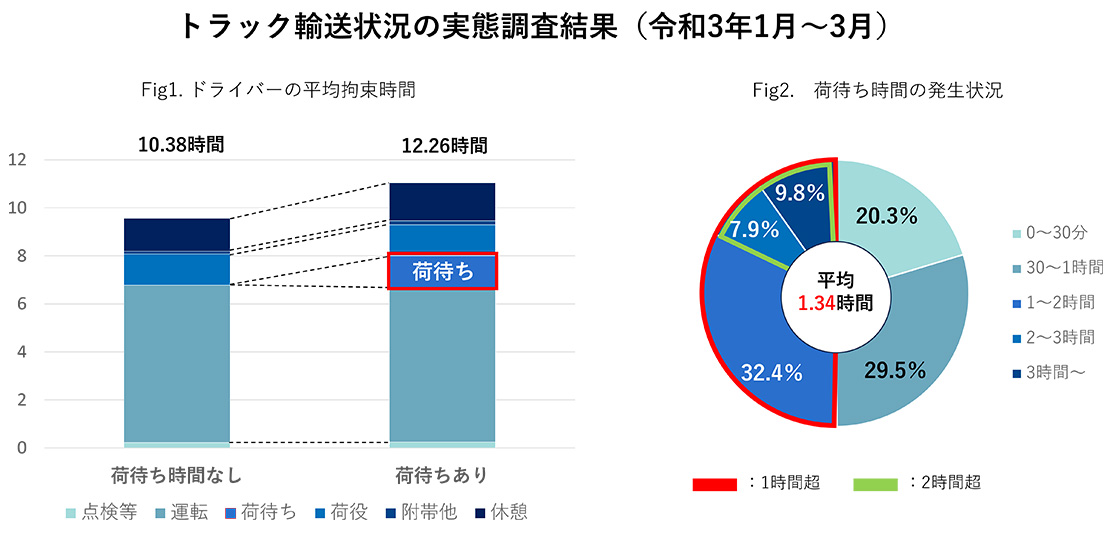
1時間を超える荷待ちは全体の約50%に達しており、更に1運行あたり2時間を超える荷待ちは全体の約18%となっているのが現状です。このような荷待ち時間の長期化は「トラックドライバーの労働環境の悪化」「物流コストの増大」につながる深刻な問題となっているのが明らかです(Fig2)。
トラックバースで荷待ち時間が発生する原因
トラックバースで荷待ち時間が発生する主な原因には、主に以下5つの原因が挙げられます。
トラックバースで荷待ち時間が発生する原因
- 到着時間が管理しづらい
- 倉庫内作業との非効率な受け渡し
- 入荷と出荷を同時に行っている
- 人材不足
- バース周辺のレイアウト
これらの要因が複合的に絡み合うことで、トラックの到着時間が集中し、倉庫内の作業がスムーズに行えません。結果として、トラックバースで長時間の荷待ち時間が発生することにつながります。
到着時間が管理しづらい
トラックの到着時間が管理しづらいことは、荷待ち時間が発生する大きな原因の一つです。計画通りの時間にトラックが到着しないことで、荷役作業の開始が遅れてしまうためです。しかし、トラックの運行は、道路の渋滞状況や天候・ドライバーの休憩時間など、さまざまな要因に左右されます。正確な到着時間の予測が難しいのが実情です。
トラックの到着時間を正確に管理するためには、配車計画の精度を高める努力が欠かせません。過去の運行実績データの分析や、リアルタイムの交通情報の活用などによって、より現実に即した配車計画を立てることが求められます。また、バース予約システムを導入し、到着時間を事前に登録してもらうことで、タイムスケジュールの平準化を図ることも有効です。
倉庫内作業との非効率な受け渡し
倉庫内のピッキング作業とトラックバースでの荷役作業の連携が取れていないことも、荷待ち時間が発生する原因の一つです。トラックが到着しても倉庫内の出荷品が準備できていない、反対に倉庫内の作業が終わっているのにトラックが来ないといったミスマッチが起こると、荷待ち時間が長くなってしまいます。
倉庫内作業との非効率な受け渡しを解消するためには、リアルタイムの在庫情報や作業進捗状況の可視化が重要です。倉庫管理システム(WMS)を導入するなど、倉庫内作業とトラックバースでの荷役作業の同期を図るための対策を検討すべきでしょう。
トラックバースでの荷待ち時間を解消する方法とは?
- 到着時間が管理しづらい
- 荷主側の準備が間に合っていない
- 入荷と出荷を同時に行っている
- 複数のトラックが同時に来場する
トラックバース問題の解消のヒントをPDF資料でご紹介
-
トラックバース予約システムとは?基礎と選び方、導入手順とおすすめ製品
トラックドライバーの長時間労働の要因となるトラックバース問題を解決する方法
入荷と出荷を同時に行っている
入荷と出荷を同じバースで行っていることも、荷待ち時間が発生する原因の一つです。限られたバース数の中で入荷と出荷を同時に行おうとすると、1か所に作業が混み合ってしまいます。トラックが出荷を終えたあとも、次の入荷トラックが来るまでバースを塞いでしまうため、全体の回転率が下がってしまいかねません。
入荷と出荷における問題を解決するためには、入荷専用バースと出荷専用バースの分別が有効です。バースを用途別に使い分けることで、入荷トラックと出荷トラックが交錯することなく、スムーズな荷役作業が行えるようになります。また、バース数に余裕がない場合は、入荷と出荷の時間帯をずらすことで、作業が混み合うのを回避するといった工夫も考えられます。
人材不足
昨今の物流業界では、トラックドライバーや倉庫作業員の不足が深刻化しており、トラックバースの荷役作業の遅れにもつながっています。例えば人手不足によって、トラックの荷卸しや積み込みに時間がかかる、倉庫内のピッキング作業が滞るなど、全体的なオペレーションの効率が落ちています。
人材不足による問題を軽減するためには、作業の自動化や省力化の促進が重要です。例えば、コンベヤーや自動ラック、AGVなどの荷役機器を導入することで、人の手を介さずに荷物を運べるようになります。また、ピッキング作業のデジタル化を進めることで、作業指示や進捗管理の効率化を図ることもできるでしょう。
バース周辺のレイアウト
トラックバース周辺の道路が狭い、駐車スペースが不足している、といったケースも荷待ち時間が発生する原因の一つです。道路の幅が狭いと、トラックの出入りがスムーズに行えなくなります。また、駐車スペースが足りないと、指定スペース以外に駐車してしまうことになり、他の車両の通行の妨げになる可能性があります。
この問題を解決するためには、敷地内の動線の見直しが重要です。例えば、荷役作業がスムーズに行えるよう、一方通行規制を設けるなどの工夫が挙げられます。
また、敷地内にトラックの待機場所を設けることで、荷役前後の一時的な駐車スペースの確保にも有効でしょう。敷地に余裕がない場合は、近隣の土地を借りるなどして、駐車場の整備を検討するのも一つです。
トラックバースの荷待ち時間を解消する方法
トラックバースの荷待ち時間を解消するためには、以下のようなシステムの導入が有効です。
バース予約システム | Webブラウザやスマートフォンアプリから予約の登録・変更が可能で、リアルタイムでバースの稼働状況を確認できるシステム。トラックの到着時間を予約制にすることで、バースの混雑緩和につながる。 |
---|---|
倉庫管理システム(WMS) | 倉庫内の在庫管理、ピッキング作業、フォークリフトの動線管理などを一元的に管理し、作業の効率化を実現するシステム。倉庫内作業とトラックバースでの荷役作業の連携を最適化する。 |
在庫管理システム | 倉庫内の在庫数量や保管場所、入出荷履歴などをデータベース化し、リアルタイムに在庫状況を把握できるシステム。在庫の可視化によって、適切な入出荷計画の立案を支援する。 |
EDIシステム | 受発注や出荷指示、納品書などといった物流事業者同士での取引情報を、電子的に交換するためのシステム。事務作業の効率化とペーパーレス化を実現できる。 |
検品システム | 納品物のバーコードをスキャンしたり、カメラで撮影した画像から品番や数量を自動で読み取ったりすることで、目視確認の手間を削減できるシステム。バーコードや画像認識技術を活用することで、検品作業を省力化する。 |
荷待ち時間の解消において、特に優先的に検討すべきなのは、バース予約システムと倉庫管理システム(WMS)の導入です。バース予約システムは、トラックの到着時間を平準化することで、荷役作業の効率化に直結します。WMSは、倉庫内作業とトラックバースでの荷役作業の同期を図ることで、荷待ち時間の短縮につながるでしょう。
トラックバースでの荷待ち時間を解消する方法とは?
- 到着時間が管理しづらい
- 荷主側の準備が間に合っていない
- 入荷と出荷を同時に行っている
- 複数のトラックが同時に来場する
トラックバース問題の解消のヒントをPDF資料でご紹介
-
トラックバース予約システムとは?基礎と選び方、導入手順とおすすめ製品
トラックドライバーの長時間労働の要因となるトラックバース問題を解決する方法
バース予約システム
バース予約システムとは、トラックバースの到着時間を事前に予約することで、トラックの到着が特定の時間帯に集中することを防ぎ、バースの混雑を緩和し、荷待ち時間の短縮を図るためのシステムです。
ドライバーがWebブラウザやスマートフォンアプリから到着時間を登録することで、倉庫側では予約状況をリアルタイムで把握できます。これにより、バースの稼働状況を可視化し、効率的なオペレーションを計画することが可能です。
バース予約システムの導入は、トラック待ちが頻発している企業や時間指定の厳しい納品を扱う企業にとって、特に優先度が高いといえます。
ただし、バース予約システムを導入する際は、ドライバーへの周知と教育が必須です。予約方法や変更ルールを明確に定め、ドライバーが確実に予約を行えるようにサポートが必要となります。また、倉庫側でも、予約状況に応じて柔軟にオペレーションを調整できる体制を整えておくことが重要です。
倉庫管理システム(WMS)
倉庫管理システム(WMS)は、倉庫内のオペレーションを一元管理するシステムです。入荷から出荷までの一連の作業をシステム上で管理することで、作業の効率化と最適化を図れます。在庫の位置情報や数量、入出荷の履歴・ピッキング作業の指示など、リアルタイムで把握・コントロールが可能です。
WMSの導入は、多品種の商材を扱う企業や入出荷の回転が速い企業にとって、特に優先度が高いといえます。在庫の見える化により倉庫内のスペースを有効活用しながら、適切な在庫配置を実現できます。また、ピッキング作業の効率化により出荷にかかる時間を短縮できるため、トラックバースでの荷待ち時間の削減にも期待できるでしょう。
ただし、WMSを導入する際は、倉庫内のレイアウトや作業動線の見直しが必要になる場合があります。システムに合わせて倉庫内の設備や運用ルールを改善することで、WMSの効果を最大限に引き出せます。倉庫作業員へのトレーニングも欠かせません。
在庫管理システム
在庫管理システムとは、倉庫内の在庫をリアルタイムに可視化し、適切な在庫水準の維持を支援するためのシステムです。在庫の数量や保管場所、入出荷の履歴などをデータベース化することで、正確な在庫情報を把握できます。これにより、過剰在庫や欠品のリスクを低減し、倉庫スペースの有効活用と、オペレーションの効率化を図れます。
在庫管理システムの導入は、在庫回転率の高い企業や、需要変動の大きい商材を扱う企業にとって、特に優先度が高いです。在庫の偏りを防ぐことで、倉庫内のオペレーションもスムーズになり、結果的にトラックバースの稼働率向上にも期待できます。
ただし、在庫管理システムを導入する際は、倉庫内の商材の特性を十分に考慮しなければいけません。また、在庫情報の精度を維持するためには、入出荷時の確認作業を徹底し、システムへの入力を確実に行うことが重要です。
EDIシステム
EDIシステムとは、物流事業者同士での取引情報を、電子的に交換するためのシステムです。受発注や出荷指示、納品書などの各種書類をデジタルデータ化しネットワークを通じてやり取りすることで、事務作業の効率化とペーパーレス化を実現します。
大量の事務処理を伴う企業や、取引先との連携を強化したい企業にとって、EDIシステムの導入は特に優先度が高いです。紙の書類のやり取りに比べデータの送受信がスピーディーになるため、トラックバースで発生する事務処理のリードタイムを大幅に短縮できます。
また、入力ミスや書類の紛失などのリスクも低減されるため、業務の正確性の向上に期待できるでしょう。
ただし、EDIシステムを導入する際は、双方が対応可能なデータフォーマットやシステムを決める必要があります。自社内の業務フローやシステムとの連携も重要であり、インターフェースの設計と開発が必要です。
検品システム
検品システムとは、納品物の検品作業を自動化するためのシステムです。バーコードリーダーや画像認識技術を活用することで、納品物の品番や数量、品質などを自動で確認し、目視による検品作業を省力化します。
作業の進捗管理や品物の期限管理も可能です。検品にかかる時間を大幅に短縮できるため、トラックバースでの荷役時間の短縮や人材不足の軽減にも期待できるでしょう。
検品システムの導入は、アイテム数の多い納品物を扱う企業や、納品物の検品に手間がかかっている企業にとって、特に優先度が高いです。
ただし、検品システムを導入する際は、納品物の特性に合わせたシステム設計が必要になります。例えば、バーコードの種類や貼付位置、商品パッケージのデザインなどによって読み取りの精度が変わってくるため、事前のテストと調整が欠かせません。また、画像認識技術を活用する場合は、商品マスタデータとの連携が重要です。
トラックバースでの荷待ち時間を解消する方法とは?
- 到着時間が管理しづらい
- 荷主側の準備が間に合っていない
- 入荷と出荷を同時に行っている
- 複数のトラックが同時に来場する
トラックバース問題の解消のヒントをPDF資料でご紹介
-
トラックバース予約システムとは?基礎と選び方、導入手順とおすすめ製品
トラックドライバーの長時間労働の要因となるトラックバース問題を解決する方法
まとめ
トラックバースにおける荷待ち時間の解消は、物流業界における大きな課題です。荷待ち時間が発生する原因としては、トラックの到着時間管理の難しさ、倉庫内作業との非効率な連携、入出荷の同時進行、人材不足、バース周辺のレイアウト不備などが挙げられます。
これらの課題に対応するためには、バース予約システムや倉庫管理システム(WMS)、在庫管理システム、EDIシステム、検品システムなどの導入が有効です。特に、バース予約システムとWMSは、荷待ち時間の解消に直結する重要なシステムといえます。
荷主企業、物流事業者、倉庫事業者が一体となって、荷待ち時間の解消に向けた取り組みを進めていくことが重要です。IoTやAIなどのテクノロジーを活用しながらトラックバースにおけるオペレーションの最適化を図っていくことが、これからの物流業界に求められるでしょう。