検品作業を効率化するコツは?課題解決方法や業種別の改善事例を紹介
お役立ち情報
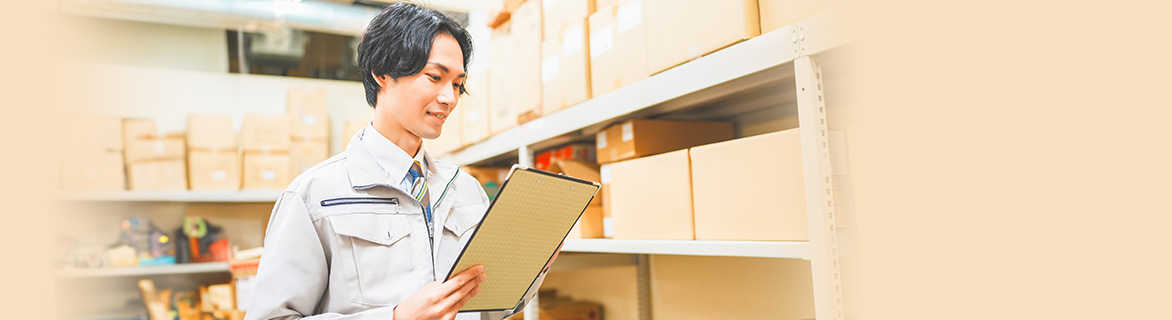
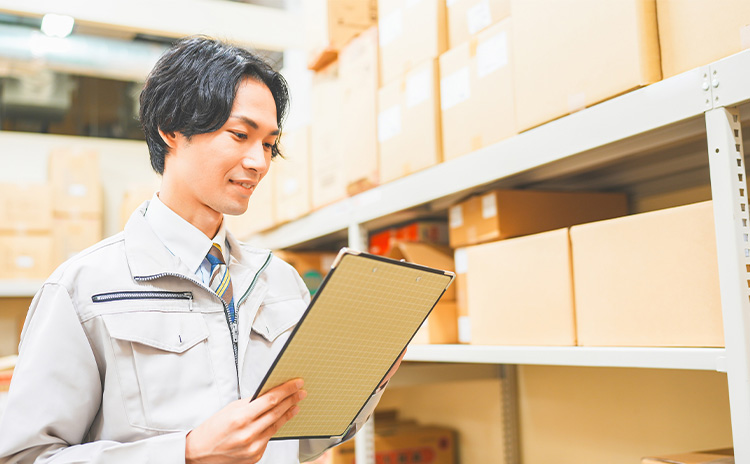
入荷時や出荷時の個数管理のために行われる検品において、ミスを減らしたり効率を上げたりしたい方も多いのではないでしょうか。実際に検品作業の効率化にはさまざまなコツがあり、課題の解決方法は業種などによって異なります。
この記事では、検品作業を効率化するコツと解決方法について詳しく解説していきます。実際に検品業務の効率化に成功した企業の事例も挙げているので、こちらも確認しながら業務改善をイメージしてみましょう。
目次
-
検品作業の種類
- 入荷検品
- 出荷検品
- 検品とピッキングの違い
-
検品作業でよく見られる2つの課題
- 検品ミスが多い
- 検品作業の効率が悪い
-
検品の課題を解決に導く3つの方法
- バーコードやQRコードを導入する
- RFIDを導入する
- 検品作業を外部に委託する
-
検品作業効率化の成功事例3選
- 工場での改善事例
- 物流業での改善事例
- 医療機器販売業での改善事例
-
検品作業を効率化する際によくある質問
- 開発経験者が社内にいなくても導入できますか?
- バーコードを使用していないのですが効率化は可能ですか?
- まとめ
検品作業の種類
検品作業の種類は大きく分けて入荷検品と出荷検品に分けられます。入荷検品は製品の品質や数量の確認を、出荷検品では品質管理と正確な出荷の確認をそれぞれ行うものです。下記のそれぞれの検品作業について役割やプロセスを詳しく解説します。
- 出荷検品
- 入荷検品
- 検品とピッキングの違い
各過程での作業内容について再確認しておきましょう。
入荷検品
入荷検品とは、リスト通りの商品がきちんと入荷したかどうかを確認する作業で、基本的には以下の項目を確認します。
- 商品が正しいものか
- 数量は合っているか
-
※
同時に商品の見た目や品質に問題が無いかを確認するケースもあります。
倉庫などでは倉庫管理システムを導入しているケースも多く、納品書や伝票ではなく入荷予定データと現物を照らし合わせて確認します。
入荷検品でミスが発生すると実在庫と理論在庫に不整合が発生し、在庫管理業務全体に影響を及ぼします。このため、入荷検品は正確な在庫管理をする上で重要です。
出荷検品
出荷検品は、注文内容をもとにピッキングされた商品が出荷指示書と相違ないか確認する作業で、基本的には以下の項目を確認します。
- 商品が正しいものか
- 数量は合っているか
-
※
同時に商品の見た目や品質に問題が無いかを確認するケースもあります。
出荷検品でミスが発生すると誤出荷となり、顧客の信用を失ってしまいます。また、内部的にも実在庫と理論在庫に不整合が発生します。このため、出荷検品は正確な発送を行う上で重要です。
検品とピッキングの違い
検品とピッキングの違いについては下記の通りです。
検品 | 商品が適切な状態かを検査する業務 |
---|---|
ピッキング | 倉庫などから必要な商品を集める作業 |
どちらの作業もスピードと正確性が求められますが、検品は商品が適切な状態かどうかを確認する目的で、ピッキングは正確な商品の選択と包装・収集が目的です。効率的な在庫管理では、検品とピッキングを組み合わせて、スムーズかつ効率的な在庫管理を実現しています。
検品作業でよく見られる2つの課題
商品の入出荷時の検品では、大量の商品の動きを早く正確に把握しなければなりません。以下のような課題に直面している検品作業者も多いのではないでしょうか。
- 検品ミスが多い
- 検品作業の効率が悪い
それぞれの課題について詳しく解説していきます。
検品ミスが多い
入荷検品時には数え間違いや転記ミスが、出荷検品時には誤った商品がピッキングされるミスなどがそれぞれ頻発しています。似たようなアルファベットや数字が羅列されている品番を見て、照らし合わせる作業には集中力や体力が必要です。製品の数や種類が増えるほど、ミスは発生しやすくなるでしょう。
さらに、紙に記載した内容をPCに転記している場合、転記時の入力ミスも考えられます。目視と手書きによる検品を行う以上、これらのミスを完全に防ぐことは現実的ではありません。特に大量の在庫や見た目が似ているような製品においてはより深刻になるでしょう。
検品作業の効率が悪い
商品がどこにあるか分からずピッキングに時間を要する点や、ダブルチェックに複数人が必要な点などから、検品作業の効率化に課題を抱える事業者も多いのではないでしょうか。
たとえ検品担当者を増員したとしても、作業内容が変わらなければ結果として業務の効率化には結びつきません。また、検品担当者を多く雇うほど、多額の人件費もかかります。
検品の課題を解決に導く3つの方法

検品を担う現場では「ミスの削減」と「効率化」が課題ですが、これらを同時に解決する方法として下記3つの方法が挙げられます。
- RFIDを導入する
- バーコードやQRコードを導入する
- 検品作業を外部に委託する
それぞれの方法について詳しく解説します。
バーコードやQRコードを導入する
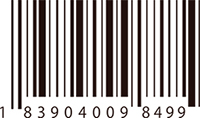
商品自体や商品が格納されている箱や棚に、バーコードやQRコードを貼り付け、それらをハンディターミナルで読み取ることで在庫を管理する方法です。
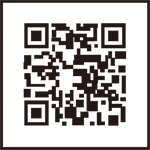
ハンディターミナルでの読み取りにより、すべての製品情報を確実に管理できます。
通信機能付きのハンディターミナルを導入すれば、リアルタイムに入出荷情報を把握可能です。従業員によるヒューマンエラーや時間のロスを削減し、効率的な在庫管理ができるようになるでしょう。
バーコードやQRコードを用いての在庫管理は、導入コストが低い傾向にあるため、コストを抑えたい方におすすめです。
バーコードは商品に予め印刷されているものを活用するほか、バーコード作成機能を含めたパッケージ製品では自作もできます。
QRコードはバーコードよりも記録できる情報量が多いですが、バーコードと比較すると読取り機器が高価な傾向です。
それぞれメリットがあるので、状況に応じながら選びましょう。
RFIDを導入する
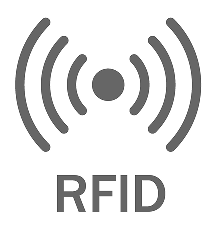
RFIDとは電波を用いてタグのデータを非接触で読み書きする技術です。RFIDは、非接触での情報読み取りが可能で、商品を箱から出したり一つひとつスキャンしたりする手間を省ける点がメリットです。また、万が一紛失した際には探知ができる点でも、バーコードやQRコードより優位性があります。
ただし、バーコードやQRコードと比べると、読み取り装置やタグの導入コストが高い傾向です。さらに導入までに「システム開発」や「タグの準備/タグ取付け等」が必要で、時間を要します。
RFIDは、導入にコストと時間がかかる分、業務効率化に大きく貢献します。予算や時間をかけられる場合は検討しましょう。
検品作業を外部に委託する
一方で、外部委託費用としてコストがかかる点や、取り扱う製品に変更があった場合、その都度製品の説明が必要な点は、デメリットとして挙げられます。
外部への委託は、3PL事業者やフルフィルメントサービス事業者に業務を委託することで効率化を図る方法です。
専門業者は、経験豊富なスタッフや豊富な支援実績とノウハウを備えているため、検品作業の質は保証されるでしょう。また外部に委託することで、繁忙期や閑散期などに応じて適切な人員の確保が可能です。さらに、検品に必要な設備投資や社内での人員確保も必要無いため、空いたリソースを本業に充てることで、本業に集中できる点も大きなメリットでしょう。
加えて、万が一トラブルが発生した際の責任の所在については、事前のすり合わせが欠かせないので、注意しましょう。
検品作業効率化の成功事例3選
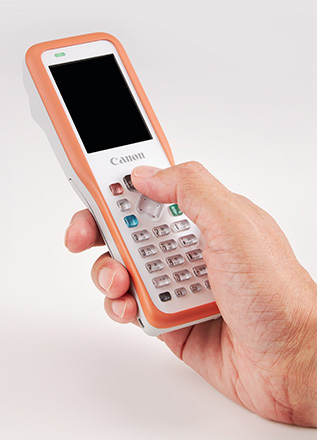
ここまで、ツールの活用により検品作業を大幅に効率化できると解説してきました。では、検品ツールを導入した企業はどのようにして効率化を達成できたのでしょうか。
ここからはバーコードとハンディターミナルを導入し、検品作業の効率化に成功した事例として、工場・物流業・医療機器販売業での事例を1つずつ紹介します。現状の検品作業で効率面に不安を抱く方や、検品作業の効率化に対するイメージを掴みたい方は、ぜひ参考にしてみてください。
工場での改善事例
PCを製造する工場では、部品の入出荷管理にハンディターミナルを活用しています。ハンディターミナルの導入によって、部品1点の検品に要する時間をおよそ70%短縮できました。作業時間が短縮されたため、従業員の残業時間の削減や身体的負担も軽減されるなど、効率化による効果が表れています。
さらに、読み取り漏れや相違があった際は、ハンディターミナル上にエラー表示が出るため、ミスの撲滅にもつながっています。作業が簡易的になり、効率性だけでなくミスの削減にも成功した事例です。
物流業での改善事例
ある物流会社では、以前は製品に貼りつけた紙と管理台帳を照らし合わせながら、手作業で検品を実施していました。加えて誤出荷防止のために2名体制でのダブルチェックを実施しており、従業員に負担がかかる点が課題でした。
そこでハンディターミナルを導入し、製品に貼られている既存のバーコードを出荷時に読み取る方式に変更しました。その結果、管理台帳を見ながらの検品がなくなり、作業工数の大幅削減と誤出荷防止を同時に実現したのです。従業員の負担も軽減され、誰が検品作業をしても同じ品質が確保されるようになりました。
医療機器販売業での改善事例
そこで、キヤノンの業務バーコード化アプリパックで、医療材料用のバーコードを読み取れるアプリを導入したところ、既存の医療材料用バーコードから、有効期限とロット番号を読み取れるようになりました。
販売管理システムに在庫管理のオプションを追加して対応しようとするも、医療材料が入った段ボールに貼られている国の規格で定められたバーコードラベルは、既存のシステムでは読み取れないことが発覚したのです。
ある医療用品商社ではこれまで、検品を目視で実施した上で帳簿に記入し、そのデータをPCに手入力していました。しかし、カウント時や転記時のミスが多く、毎週実施する棚卸で在庫数が合わない課題を抱えていました。
入荷時に新たにバーコードを生成し貼り付ける作業の削減や、出荷時に有効期限切れチェックができるなど、検品作業の効率化に成功した事例です。
検品作業を効率化する際によくある質問
バーコードでの検品電子化を検討中の方から、よく寄せられる下記の質問に回答します。
- 開発経験者が社内にいなくても導入できますか?
- バーコードを導入していないのですが効率化は可能ですか?
ハンディターミナルとバーコードの導入は、手軽で柔軟性があり、特に開発経験がなくても取り組めます。
開発経験者が社内にいなくても導入できますか?
開発経験者がいなくても問題ありません。キヤノンの「KNTool」では、安く・早く・簡単に在庫管理の電子化を実現できます。KNToolの特長は下記の通りです。
- ノーコードでアプリケーションを開発できるため、開発経験が無くても内製化が可能
- 開発工数を大幅に短縮し、業務に応じたアプリケーションの開発が可能
- エミュレータ機能搭載で、PC上で簡単に動作確認が可能。
コストを抑えつつ迅速な導入が可能で、社内に検品ツールの開発経験者がいなくても安心です。
バーコードを使用していないのですが効率化は可能ですか?
キヤノンの「KNTool」には、市販のラベル紙に対応したバーコード作成ソフトが同梱されており、独自のバーコードの作成・運用が可能です。
バーコードの作成や貼りつける作業は必要ですが、最初にバーコードが利用できる体制を整えれば、その後は効率的な運用ができます。
まとめ
検品作業の効率化には、バーコードとハンディターミナルを導入した電子化がおすすめです。これらの導入により、検品業務の効率化と人的ミスの削減を同時に実現できます。
バーコードを使用した検品に興味がある方、こんなことはできないの?と疑問をお持ちの方、ハンディターミナルやKNToolを実際に触ってみたい方は、お気軽にお問い合わせください。
こちらのお役立ち情報をダウンロードする
関連情報
エッジデバイスソリューションについてのご相談・お問い合わせ
キヤノンマーケティングジャパン株式会社 エッジデバイスソリューション企画部